January 1956 Popular Electronics
Table
of Contents
Wax nostalgic about and learn from the history of early electronics. See articles
from
Popular Electronics,
published October 1954 - April 1985. All copyrights are hereby acknowledged.
|
Something that is always in the forefront of
my mind when reading these articles from vintage American electronics magazines
is how most of the products - including even the smallest components - were made
in the United States. When I read vintage British electronics magazines (e.g.,
Wireless World), most of the products were produced in Europe.
The technical and manufacturing know-how was spread throughout the regions of the
Earth where its citizens dreamed up and realized the wonders that made the modern
world. Part of the reason is supply and distribution chains were not as capable
due to communications and transportation limitations. Nowadays, it seems almost
nothing is made in the countries where the products are designed - except in places
like China where so much technology has been exported to there that their people
(very smart folks) are now designing and manufacturing their own products. Consequently,
a large portion of the population in the U.S., England, France, Germany, etc., no
longer has the skills to do the job. They don't have any idea how such things are
accomplished since for most (or all) of their lives almost everything they own
has come
with a "Made in China, or Vietnam, or Myanmar, or Chile, etc." marked on it. As
late as the early 2000s, fairly stringent technology export restrictions still
were in place in order to keep the latest and greatest capability here at home
for strategic purposes, but it seems almost nothing is protected anymore.
Apologies for the lousy pictures - the originals in the magazine were crapola.
Image Orthicon
Expert care, precision equipment, and a
dust-free atmosphere are required in making TV camera tubes
Factory Production of image orthicons - the all-important television camera tube
- is under way in ultra-modern facilities at the General Electric plant, Schenectady,
N. Y. Technicians work in nylon clothes and use hospital-clean glass lathes and
punch presses, as well as a variety of electrochemical equipment, all behind sealed
doors in air-filtered rooms.

Precision welding operation joins a 500-wire mesh to the metal
ring. The glass bubble, ring, and wire mesh assembly form a critical part of the
finished TV camera tube. Mesh cannot touch glass bubble. but must remain spaced
from it at 0.002·lnch distance.
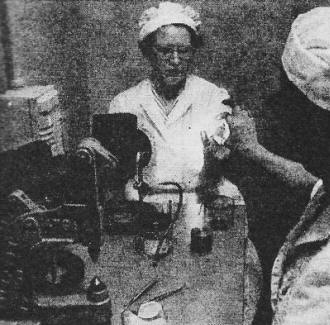
Technician receives the glass target and wire mesh assembly after
every speck of dust has been removed.

The assembly is inserted into the glass tube which eventually
becomes the image orthicon. Technician lightens setscrews to hold target in correct
position.
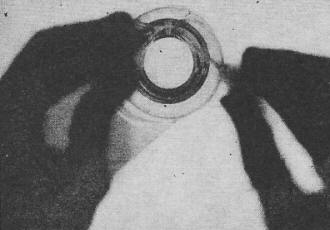
View of the target is what the assembler sees as she works with
thin, 18-inch offset screwdriver fastening the target assembly in place within the
glass tube. One slip of the screwdriver could shatter the glass membrane. rendering
the tube useless. A speck of dust might not show up until the tube was completed,
which would be too late to save the tube.
This million-dollar investment in camera tube manufacturing involves the assembly
of 256 parts to make a single tube. The operation requires exceptionally high dust
and lint control standards. In addition, it calls for handicraft skills comparable
to those used by artisans of centuries past.
Heart of the image orthicon is the "target and mesh assembly." Difficult to make
and install, it consists of a perfect copper mesh of 500 wires to the inch. This
mesh must be spaced two-thousandths of an inch from a delicate glass membrane. The
membrane, or "target," must be between one-tenth and two-tenths of a thousandth
of an inch thick.
The entire assembly is then inserted into the 13" stem of the tube and. fastened
in place with screwdrivers that are 18" long. This must be accomplished without
either breaking the glass or permitting even the tiniest speck of dust to enter
the tube.
Despite the critical nature of this assembly, the General Electric Company is
managing to produce the tubes in quantity. In addition, G. E. is looking forward
to mass production of the less expensive - and less critical - vidicon camera tubes.
Expected to be employed in large quantities as closed circuit television develops
in the next five years, their use is anticipated in military, industrial, commercial,
administrative, and home applications.

Fragile section of glass bubble - about 0.0001·inch thick - is
carefully placed on metal ring. It is then sealed to ring in oven to form delicate
"target" of an image orthicon.

The critical nature of the work is suggested by signs on the
door. A sneeze, cough, or unsteady nerves here could cost up to a thousand dollars
as technician finishes assembly of camera tube.
Posted February 12, 2024 (updated from original post on 1/2/2017)
|