May 1955 Popular Electronics
Table of Contents
Wax nostalgic about and learn from the history of early electronics. See articles
from
Popular Electronics,
published October 1954 - April 1985. All copyrights are hereby acknowledged.
|
I find it interesting
that "Project Tinkertoy," so dubbed by the National
Bureau of Standards (NBS -
now the National Institute of Standards and Technology,
NIST), does not contain a trademark to acknowledge the
ownership of the
Tinkertoy™ name. This 1955 Popular Electronics story doesn't mention
it, either. Tinkertoy has been around since 1914 and every boy I knew in my
neighborhood had at least one set - usually received as a Christmas gift. I had
a couple of them, as well as an
Erector Set or two. That said, I believe that a more
appropriate name for the endeavor would have been "Project
Lego™" because of the
way component blocks snap and stack together (with the help of a little solder).
Legos entered the toy realm in 1949. Various incarnations of the Tinkertoy
or Lego concept for modular electronics has been tried over the years, but none
have really become popular from a commercial perspective other than as
components of experimenter prototyping sets. In fact, the current
Maker
rage using
Arduino kits with their associated functional blocks can be
considered such a concept.
Project Tinkertoy
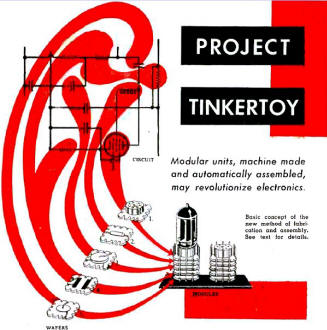
Basic concept of the new method of fabrication and assembly.
See text for details.
Modular units, machine made and automatically assembled, may revolutionize electronics.
"Project Tinkertoy" - the revolutionary modular design and mechanized production
of electronic parts - may well comprise the building blocks of the electronic world
of the future.
Developed by the National Bureau of Standards, Washington, D. C., this new approach
to electronic fabrication involves the "modular design concept" of mounting adhesive
carbon resistors, printed circuits, and other miniaturized components on standard,
uniform steatite (ceramic) wafers. The wafers are then stacked together, like building
blocks, to form a "module." This module will perform all the functions of one or
more electronic stages. It is a standardized, interchangeable subassembly with all
the requirements of an electronic circuit, plus the factors of ruggedness, reliability,
and compactness.
Individual modules may be combined to form major electronic subassemblies.
Until recently, the modules were assembled by hand. In fact, several private
industrial plants are experimenting with this method. But recently, scientists at
the National Bureau of Standards have enhanced this approach to electronic manufacture
by setting up a completely mechanized production line not only for making the small
parts and the wafers, but for putting them together to form the modules. A machine
has been developed which stamps out 2800 wafers every hour. The wafers then receive
the prefabricated parts automatically. Resistors, capacitors, etc., are being made
by completely new methods, involving special chemicals and ingenious mass-production
techniques. For example, resistors are made by coating a long roll of paper tape
with a special adhesive powder. After further processing, the tape is slit and cut
to produce desired resistances of from 10 ohms to 10 megohms. A 75-foot roll of
tape will produce over 10,000 resistors!
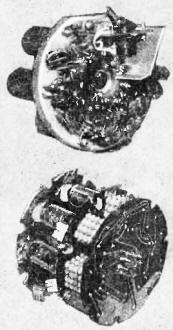
Photo above compares conventionally made piece of equipment (upper
unit) with same piece made by "Tinkertoy" methods. Latter was made in less time
at lower cost. Resultant savings can be passed on to public.
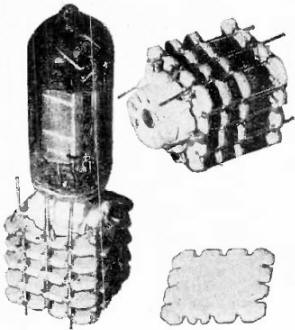
Module consists of wafers bearing miniaturized parts and printed
conducting circuits.
During the automatic mounting of resistors, capacitors, coils, tube sockets,
etc., onto the wafers, photo-electric devices along the line control flow and assembly.
Tubes are mounted in their sockets by a machine which places the tube pins in
their correct holes. A wafer is then riveted to the socket. Automatic soldering
of all parts requiring solder is provided.
Uniform wafer-mounted parts are then combined into a functional electronic unit,
or module, by a single machine, which automatically wires and solders the wafer
units into a complete module. These module assemblies are then hand-mounted on base
plates to form different types of radio and other electronic equipment. One base
plate with six modules, for instance, contains all the circuitry needed for a 6-tube
radio receiver.

Machines make ceramics, process and apply parts to wafers, assemble
modules, and perform complete inspection.
Studies of these methods made by private industry indicate that the "Project
Tinkertoy" approach may prove to be cheaper and superior in many other ways to existing
production methods. Originally developed for U. S. Navy equipment, these new methods
may result in better built, less expensive consumer goods for all.
Posted August 21, 2019
|