Not many people rewind transformers
these days, but then even in 1955 when this "Design Tips for Rewinding Your
Own Transformers" article appeared in Radio News magazine not many
were rewinding transformers. Plenty of radio repair servicemen did, though,
because replacements were expensive and getting replacements for other than
common transformers could take a long time. There was no searching for one on
the Internet and having it delivered in a couple days. Since many - if not most,
by necessity - electronics repair shops kept subscriptions to available trade
magazines, publishing an article like this provided a great service. Author
James Dolan provides all the necessary information for either designing your
own transformer from scratch or for modifying an existing transformer to meet
your specific requirements. Many shops kept a topically arranged index card
file listing the magazine name, issue number, and article title for quick reference.
Design Tips for Rewinding Your Own Transformers
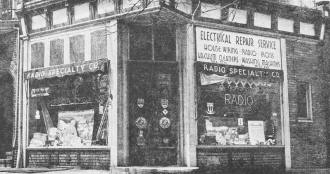
Many servicemen must, of necessity, rewind small, defective
radio transformers in view of present-day shortages.
By James E. Dolan
Save those old transformer cores. Many of them can be used for self-designed
units for special jobs.
Lack of priority, special experimental work, urgency, a desire to design
and construct your own transformer, any of these reasons may lead you to attempt
the design and the construction of your own transformers. This article is intended
to assist the prospective transformer builder who has been saving a stock of
cores with the intention of making something out of them someday. To the constructor
of transformers is opened the possibility of constructing transformers for his
own special uses, to his own specifications, and in whatever electrical size
he wishes.
As the experimenter generally plans to use cores which he has on hand, whether
they be from some old discarded broadcast job, or something he overloaded once
too often, or the parts of a pole transformer gained by a wise alliance with
some local power company, this article will attempt to show how those cores
can be put to good use.
The first consideration is the size of the
cores on hand, both physical and electrical. Get a little notebook and then
measure all of the cores on hand, putting this information into your notebook.
Our first consideration of design will be the wattage of the transformer we
are planning to make. Accordingly, it would be wise to list our transformer
core stock in regards to the wattages which they will carry. Also listed, should
be the thickness of the core, the cross-sectional area of the center leg if
the core is of the shell type, and the cross-sectional area of one leg if it
is of the core type. The area and length and width dimensions of the window
in the core into which the completed coils must fit should also be recorded.
It is quite disconcerting to wind up a coil and then find that the window of
the core is too small to receive the completed winding. It is well to allow
10% to 40% extra space allowance in making coil size computations unless you
happen to have some sort of winding machine, such as a good lathe with proper
change gears, on hand with which to wind your coils, as otherwise you are not
going to attain the winding spaces shown in the common wire tables which give
so many turns per square inch. Do not try to squeeze the winding into the least
possible space; allow for your errors and the departure from perfection that
you are sure to make.
The only tool required for the first part of our work is a good ruler; measure
the outside dimensions of the cores, their length and width, the window area,
and the thickness of the core. Compute the cross-sectional area from these figures.
Remember to clamp the core up tightly when measuring the thickness, or an error
will result in your computation.
The wattage that the core will handle is found by reference to the graph
given for this purpose. This graph has the wattage ratings on the left-hand
vertical column and the cross-sectional area is at the base of the graph. A
curve on the graph is marked "Area to Watts." Find the cross-sectional area
. on the base scale and follow a vertical line erected at the point representing
the area up to the "Area to Watts" curve. Where this vertical line meets the
curve draw a horizontal line to the left to the wattage column. This will indicate
the wattage-handling capabilities of the core.

Fig. 1 - Follow these curves carefully when designing your
own radio transformers to obtain maximum efficiency and operating performance.
The next consideration is the use that is proposed for the cores on hand.
If a requirement for a transformer comes up, have you a core that can be used
for the purpose? That is the first question that must be answered; find the
wattage. Wattage is equal to the product of voltage and amperage, or:
W = EI ..........(1)
Thus, we must multiply the voltage by the amperage of each secondary and
add these together to find what wattage is required. Let us design and construct
a transformer which will deliver 5 volts at 3 amperes with a center tap; 6.3
volts at 4 amperes with a center tap; and have a high-voltage winding of 450-0-450
volts and which will deliver 200 milliamperes of current. The transformer will
operate on 115-volts, 60-cycle current. Applying our formula (1) we have, 5
x 3 is 15; 6.3 x 4 is 25.2; and 450 x 200 milliamperes or 0.2 ampere, is 90.
These products represent the wattages of the individual secondaries. Add them
and the total secondary wattage is the result, in this case, 130 watts. The
primary wattage is found by adding to this figure the losses in the core and
windings. Usually these losses are about 10% of the rating of the transformer.
Therefore, if we divide the secondary wattage by 0.9 we will find the primary
wattage; thus:
Wp = Ws/0.9 ....... (2)
in which Wp represents primary wattage and Ws represents
the secondary wattage.
If this is done, the primary wattage for the transformer is 144 watts. Let
us call this 150 watts in order to secure an easy working value.
We can stop right here and consult our previously made chart in our notebook
showing the cores on hand and the data on them. Have we a core on hand that
will handle 150 watts? Perhaps a sheet of silicon steel must be purchased from
a local steel dealer and cut up to make a core type transformer. Perhaps we
have a 200-watt core on hand from which we can subtract a few laminations to
use it for a 150-watt application.
Now, due to the power factor of the transformer we cannot divide this wattage
value by 115 volts in order to find the current, but must take this power factor
into account. As the power factor is generally about 90% we can find primary
current by multiplying the primary voltage by 0.9 and dividing the primary wattage
by this product.
Ip = Wp /(Ep x 0.9) ..............
(3)
If 115 volts is used for the primary voltage, this product (Ep
x 0.9) becomes 103.5; if the primary voltage is 110 volts, the product becomes
99. If we wish to secure an easy figuring value, we may call this product 100,
which would represent a primary voltage of a little over 110 volts. If we use
the factor of 100 in our proposed transformer design which has a primary wattage
of 150 watts, we find that our primary current will be 1.50 amperes.
The next step in the design is the calculation of the turns in the windings.
The graph indicates the primary turns for a 115-volt primary using a core flux
density of 75,000 lines per square inch. As all types of steel will be in the
cores that we shall use, it is necessary to pick out a value which is high enough
for good operation and still not so high as to cause excessive core losses with
the poorer grades of steel. This table is made by assuming the primary voltage
as being 115 volts and the frequency 60 cycles per second. It is easy to use
the graph; having the core area (cross-sectional) on the base line, erect a
vertical line from the base at the point representing the core cross-sectional
area to the line marked "Area to Turns." At the point where this vertical intercepts
the curve so marked, extend a horizontal line to the right-hand side of the
graph where the turns in the primary circuit will be indicated.
Going back to the proposed transformer that we are building, it is noted
again that the core has to carry 150 watts. Consulting our graph we find that
the cross-sectional area required for this power of 150 watts is 2.2 square
inches. The primary will have 270 turns of wire as shown by the "Area to Turns"
curve.
As we have the primary turns from the graph, we can find the secondary turns
for each winding by application of the formula stating that the ratio of primary
voltage to primary turns is directly proportional to the ratio of secondary
voltage to secondary turns. Mathematically this is: Ep/Np
= Es/Ns
This formula is made more usable by transposing it into a more workable form
in which the factors are changed to indicate turns per volt rather than a proportional
ratio problem. Thus, as turns per volt is the number of turns divided by the
voltage, one term of our new formula should be in this form:
Ns = Np/Ep x Es
The new formula now states that the secondary turns is equal to the primary
voltage divided by the primary turns and this result is to be multiplied by
the secondary voltage. In our proposed transformer we have found our primary
turns to be 270; substituting this value and inserting the primary voltage into
our equation (5) we have:
Ns = 270/115 x Es = Es
x 2.35.
Now, by substituting the various secondary voltages in place of Es
in our formula we can easily find our secondary turns. Our proposed transformer
has three secondaries, 5 volts, 6.3 volts, and 900 volts, all center-tapped.
Using the above formula we find that the 5-volt winding requires 12 turns; the
6.3-volt winding requires 14.8 or 15 turns; and the 900-volt winding requires
2115 turns. Center taps will be on each winding at 6, 7 1/2, and 1058 turns
respectively. A small chart showing the design considerations of the various
windings should now be constructed. This chart should show primary voltage,
current, turns, wire size, and the cross-sectional area of the winding. The
same data for each secondary also will be shown. The wire insulation also should
be indicated for each winding. Returning to our proposed transformer, we found
that the core had to have 2.2 square inches of cross-sectional area. We have
on hand a core of the shell type, the center leg of which is 1 1/2-inches wide
and 1 1/2-inches thick. By removing a few laminations we can bring this core
down to 2.2 in cross-sectional area to suit our purpose. The window of this
core is 2 1/4-inches long and 3/4-inches wide. It is now our concern to find
out if our coil will fit into this window. The window area is 1.688 square inches.
It is now necessary to decide the size of wire to be used for the various
windings. In general, the wire should have a cross-sectional area of between
750 and 1500 circular mils per ampere of current to avoid excessive copper losses
and to prevent the coil from becoming overheated. By examining a wire table,
we find that No. 14 wire has a cross-sectional area of 4107 circular mils, which
is acceptable for the 3- and 4-ampere windings. The 1 1/2 ampere winding requires
a smaller wire size, so we choose No. 19 wire with a cross-sectional area of
1288 circular mils. The high-voltage winding which carries a current of 0.2
ampere should have an area of about 150 circular mils. We find that No. 28 wire
has an area of 151 circular mils, which is satisfactory for our purpose.
Our chart of wire and turns information should now be constructed and for
the transformer which we propose to construct, it is shown in Chart I. When
we add the last column of our chart we will find the cross-sectional area required
for the wire in the coil, in this instance, 0.922 square inches.
An allowance must be made for insulation which should be placed around the
core and between the windings. We shall allow 0.050 inch of thickness of insulation
for the insulation around the core; as the winding space is 2 1/4-inches long,
this means 2 1/44 X 0.050 or 0.11 square inch of insulation at this point. There
are four coils to take into consideration, the primary and three secondaries,
and between each of these will be inserted 0.025 inch thickness of insulation.
As these coils are again 2 1/44-inches long, this means that this insulation
will occupy 0.056 between each pair of coils. As there are four coils with three
spaces between them, it means that the insulation between the coils will amount
to 0.170 square inch. In addition to this insulation, a cover insulation will
be needed to cover the outside of the coil. Let this insulation be 2 1/4-inches
long and 0.025 thick; this will occupy 0.06 square inch. Each end of the coil
must be insulated. This insulation will be 0.050 thick and 3/4, wide or 0.08
square inch for both ends. The area of the insulation of the coil is the total
of all of these individual insulations, or 0.42 square inch for insulation.
Adding this insulation area to the area required by the wire will give the
total core window area needed to accommodate the coils. In our proposed design
our windings require 0.922 square inches and our insulation requires 0.42 square
inch. The finished coil will then require 1.342 square inches. We have not made
any allowances for the unevenness and other discrepancies of hand winding or
hand construction of the coil. It is necessary to make from 10% to as much as
40% allowance for winding and insulating. If you are careful, the lower percentages
will apply, otherwise, the coils should be considered as requiring 30% or 40%
of the calculated space requirements. In our present case, we will count on
being quite careful and allow 20% for extra space. This 20% of 1.342 square
inches is 0.268 square inch and adding this to our computed area we find our
complete area, with allowances, is 1.610 square inches. As the window in the
core that we have picked for this job is of ample size to accommodate this size
of winding we may proceed with our design. (Our window area is 1.688 square
inch.)

Chart I - Design considerations of the various windings.
Now find the mean length of turn of each secondary and multiply this mean
turn length by the number of turns in each secondary to find the length of wire
required for each secondary. This also applies to the primary. Record this length,
as it is our purchasing guide for our wire requirements. From a wire table find
the resistance per 1000 feet of each size of wire to be used in the various
secondaries. Calculate the resistance of the secondary windings. Multiplying
the resistance of each winding by the current passing through the winding will
give us the voltage drop in each winding. If the voltage drop is objectionable
by being too high to give us our desired characteristics of voltage and current
then add a few turns to the deficient windings to compensate for this voltage
drop. Now square the current of each winding and multiply this by the resistance
of each respective winding. This will give a product which represents the I2R
or copper loss caused by heat in the windings generated by the passage of current.
Note these copper losses and their sum as this factor will be used shortly in
computing transformer efficiency. Finding the losses present in the core of
the transformer is easily done by calculating the cubical contents of the core,
and, knowing that silicon steel weighs 0.27 lb. per cubic inch, we can compute
the weight of the core. Of course, it is also an easy matter to put the core
on a scale and read the weight if a scale is handy. Our core losses will be
about 1.7 watt per pound of core material. Multiply the weight of the core by
1.7 and the result will be the losses in the core in terms of watts. Add these
loss figures together with the copper loss and the core loss figures, and their
sum will give us the total losses of our transformer.
Take the wattage of the secondaries and multiply it by 100. Divide this product
by the same wattage plus the total losses, including both copper losses and
iron losses. This will result in a percentage factor which will be the efficiency
of the transformer. Stated mathematically:
Eff. = (Ws x 100) / (Ws + losses)
The efficiency should be about 90% or better. If you have used a smaller
wire size somewhere because you had it on hand, you may have increased the copper
loss; if the core loss seems high do not reduce the core size, rather use a
larger size wire on one or more of the windings to reduce the copper losses.
Lumping all the calculations of our last paragraph for our proposed transformer
we find, first, that our mean turn length is approximately 7 inches. There are
270 primary turns, requiring 157 feet of No. 19 enamel wire. As secondary #1
and #2 use the same size wire, we can consider both at one time, and our wire
requirement here is 16 feet of No. 14 enamel wire. Secondary #3 will require
1232 feet of No. 28 enamel wire. The resistance per foot of these wire sizes
is: 0.002525 ohm per foot for No. 14; 0.008051 ohm per foot for No. 19 enamel;
and 0.065 ohm per foot for No. 25 wire. The resistance of the various windings
are:
Primary 1.26 ohms; secondary #1, 0.018 ohm; secondary #2, 0.022 ohm; secondary
#3, 80 ohms.
The voltage drop per winding is:
Secondary #1 0.054 volt; secondary #2, 0.088 volt; secondary #3, 16 volts.
The voltage drop in secondary #3 is not objectionable. In order to compensate
for our voltage drops in secondaries Nos. 1 and 2, and to overcome the resistance
in the leads from the transformer to the sockets, we shall add one turn to each
of these windings. Thus, we give them a new value of 13 and 16 turns respectively
with the center taps now at 6 1/2 and 8 turns. Change the previously made chart
to these new values.
The current squared times the resistance of each winding is:
Primary, 2.8 watts; secondary #1 0.16 watt; secondary #2, 0.35 watt; secondary
#3, 3.2 watts. The total copper loss is 6.51 watts.
As the core has outside dimensions of 4 1/2 by 3 3/4, inches and weighs 4.6
lbs., the core losses are 7.8 watts. The total losses are the sum of the copper
and core losses or 14.3 watts. The efficiency of the transformer is:
(Ws x 100) / (Ws + losses) or (130
x 100) / (130 + 14.3)
Doing the mathematical operations indicated, we find that our efficiency
is nearly 91%. As our efficiency figure is our check on the usefulness of our
design and our efficiency is over 90% in this case, the design is fully satisfactory
and we may go ahead and construct our transformer.
Posted March 5, 2021
|