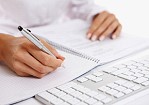
You are welcome to submit yours.
As technology and measuring
techniques advance, the time eventually comes when continuing to use old methods
not only doesn't make sense, but can actually harm your reputation by providing
data that cannot be duplicated by customers who long ago adopted the new ways. Orwill
Hawkins, of LadyBug Technologies, has written a white paper describing how to make
accurate, repeatable peak and pulse power measurements on waveforms using the precision
of modern instruments that provide a graphical view of the entity being investigated.
USB power meters provide an inexpensive means of obtaining high quality measurements
and the benefits of a graphical display environment (on your computer) at a relatively
low cost. I particularly like the use of the word 'mesial' in describing the midpoint
of a pulse's rising and falling edges.
October 2013
Application Note
Measuring Peak and Pulse Power with USB Power Sensors
By Orwill Hawkins LadyBug Technologies, LLC
Advances in computing and measurement technology have increased the capabilities
of USB RF Power Sensors.
These advances have made measurement capabilities possible at modest costs that
were previously out of reach. Capabilities like direct measurement of pulse power
can now be done with low cost USB power sensors, such as those used in the example
below. This paper will compare Pulse Power measurement using new, accurate USB Sensor
technology to traditional measurement methods.
Traditionally, Microwave Pulse Power has been measured using average power and
applying the pulse's duty cycle using the long time accepted formula:
Pulse Power = Average Power / Duty Cycle.
This method uses total measured power over time and produces a computed Pulse
Power result based on assumed pulse information. Unfortunately, additional information
such as peak power, droop, and crest factor may remain unknown, rendering the measurement
limited in value. Significant errors are also possible with this method due to errors
in the assumed pulse width and duty cycle. Errors caused by discrepancies between
actual and assumed pulse shape or malfunctioning equipment may also occur.
Given the rapid advances in modulation technology, it is important to recognize
the need for the additional information and accuracy that is now available with
today's Power Sensor technology.
Modern USB Power Sensors utilize cutting-edge processing technology and are capable
of rapidly measuring and digitizing the demodulated waveform. These sensors integrate
the measurement data over time and provide the user with actual pulse power, and
provide additional measured parameters such as peak power, crest factor and duty
cycle, in addition to average power. This information is often very useful for the
engineer, designer and technician. Figure 1 depicts a microwave pulse stream and
indicates some of the desirable information that can be measured with a USB Power
Sensor.

Figure 1 - Pulse Waveform Detail
To deliver the necessary measurements, USB Peak and Pulse sensors use advanced
trigger schemes that accurately locate the pulse mesials and process the digitized
data from the measured power. These sensors provide accurate Peak Power, Pulse Width,
Pulse Power, Pulse Repetition Rate, Duty Cycle, Crest Factor and more. As an alternative,
some USB sensors, such as the LadyBug LB480A PowerSensor+™ that was used in the
example below, support external triggering. This allows control of the measurement
timing and can be particularly useful with very low power measurements where the
signal might be near the noise floor. Averaging repetitive signals improves measurement
accuracy.
Pulse Power Example
For example purposes, pulse power was measured from a small test source. The
pulse modulating waveform has an 11 microsecond pulse width and a pulse repetition
time of 100 microseconds. The Pulse carrier frequency is 1.9 GHz, and the on/off
ratio for the test signal is better than 80 dB. Pulse power is just under 6 dBm.
The test source was connected directly to the LadyBug LB479A Peak, Pulse and Average
Sensor. The LB479A operates from 10 MHz to 8 GHz and over a dynamic range
of - 60 dBm to +20 dBm.
A screen shot of the measurement is shown in Image 1. All of these measurements
were made simply by connecting the sensor to the signal source and entering the
carrier frequency. This greatly simplifies and speeds up the measurement process
weather it is in a bench, ATE, or service environment.

Image 1 - Power Measured with a LadyBug LB479A
Analyzing the Results
The traditional method requires the user to know the signal's Duty Cycle in order
to calculate Pulse Power. Because Average only Sensors are not capable of measuring
Duty Cycle, it must be calculated using the formula below. In many cases the Duty
Cycle is given or assumed, not measured, adding suspicion to the measurements accuracy.
In this case the Duty Cycle is given as 11.0%
Duty Cycle=Pulse Width / Pulse Repetition Rate.
Calculated Duty Cycle is 11% (=11 us/100 us)
Note that the calculated 11% Duty Cycle is close to the 11.1% actual Duty Cycle
measured by the sensor. This method can lead to other inaccuracies in the measurement
caused by errors in the assumed pulse parameters, amplifier or modulator distortion,
failing components etc.
The sensor measured -3.657 dBm average power. Prior to applying the traditional
method of determining Pulse Power, the measured average power must be converted
from dBm to a linear scale, in this case mW. The following equation was used:
P mW=10^(PdBm/10) = 10^(-3.657/10) = 0.431 mW.
Now that linear power and Duty Cycle are known, Pulse Power can be calculated
using the standard traditional formula:
Pulse Power = Average Power / Duty Cycle as mentioned earlier.
Plugging in the numbers results in a pulse power of 3.92 mW or 0.431 mW/0.11.
This can now be converted back to dBm using
PdBm=10*log10(PmW)
The result is 5.933 dBm, and is very close to the more precisely measured
5.879 dBm.
For further comparison, the Sensor was replaced with a LadyBug LB480A with pulse
profiling time domain analysis capability as shown in Image 2.

Image 2 - Pulse Profile Measurement
Zoom was utilized to expand the data and three markers were placed to determine
the pulse width and repetition rate. Start time is shown by Marker #1 at 199.950 us,
Marker #2 marks the pulse's end time at 210.950 us, and Marker #3 marks the
end of the cycle at 311.100 us. The results visually and mathematically confirm
previous measurements.
Conclusion
USB Peak, Pulse and Average Power Sensors, provide a lot of the valuable information
that a Time Domain, Pulse Profiling sensor provides, at less cost. These sensors
accurately measure Peak, Pulse & Average Power plus Duty Cycle along with analysis
such as Crest Factor. The Sensors can expose unexpected system faults that cannot
be found using an Average Power Sensor. These facts make them a very good alternative
to traditional methods that utilize average only Sensors and combine the readings
with the assumed pulse parameters. Today's modern Peak, Pulse and Average Power
Sensors such as the LadyBug Technologies LB479A that was used in the example above,
are cost competitive solutions for RF engineers and technicians.
Contact Info
Orwill Hawkins LadyBug Technologies, LLC Contact Phone: 707-546-1050 x103
Website: www.LadyBug-Tech.com
e-Mail:
Orwill@LadyBug-Tech.com
Posted October 24, 2013
|