July 1951 Electronics
[Table of Contents]
Wax nostalgic about and learn from the history of early electronics.
See articles from Electronics,
published 1930 - 1988. All copyrights hereby acknowledged.
|
According to this "Auto-Sembly of Miniature Military Equipment"
article from a 1951 issue of Electronics magazine, the U.S. Army Signal
Corps first experimented with chemically photo-etched printed circuit boards
(PCBs) in 1949. Someone there got the idea from seeing the way nameplate
manufacturers created similar signs for doors, desks, equipment nomenclature
plates, etc. The authors wrote numerous articles* in numerous magazines over
about a five year period on the Auto-Sembly process whereby leaded components
are inserted into substrate through-holes, and then dipped into a solder bath as
a complete assembly. Some history on the research is provided regarding
photoresist compounds, etching mixtures, parameters of copper traces based on
foil thickness and width (resistance, current handling), and other critical
items. RF impedance measurement are not discussed since at the time only low
frequency (DC, audio, and control signals) was involved on PCBs. It is a very
interesting read.
* See also
The Design and Layout of Printed Circuit Patterns - November 1952 Radio &
Television News
Production of wiring by acid etching of copper-faced insulating
laminates permits rapid assembly of high-quality conventional JAN components by
inserting leads in punched holes, then immersing chassis surface in molten solder
to make all joints simultaneously.

1) Copper-foil-coated phenolic chassis is starting point for
Auto-Sembly of battery-powered audio amplifier (L) 2 ) Conductor pattern is applied
in acid-resistant ink by silk-screening or offset printing (C) 3) Chassis after
etching away unwanted metal in ferric chloride solution and removing resist (R)

4) Next step is punching or drilling of holes through which leads
of components are inserted from rear. (L) 5) Underside of chassis after components
are mounted and assembled by one-shot solder dip. (C) 6) Top of completed chassis,
showing layout of tubes and components, with plug-in terminals at right. (R)
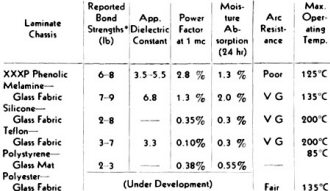
Table I) Characteristics of Copper-Faced Laminates
* Bond strengths are measured by pulling
a scored one-inch copper strip vertically away rom the laminate surface. The bond
strengths vary among manufacturers but the values shown indicate the general range
of values measured. (The bond strength of copper-phenolic is an exception, being
representative of one manufacturer's item.)

Top and bottom views of Auto-Sembled chassis containing phase-shift
oscillator, avc, and clipper/limiter circuits that serve as a unitized packaged
plug-in assembly for a complex electronic fault locator. Embedment of chassis in
casting resin will provide protection against moisture and give rigidity to plug-in
terminals at left.

Detailed view of solder-dipped pattern. Fillets at termination
points are obtained by using a waxy flux. Long protruding leads go between components
and into holes in next layer.

Experimental five-stage impedance-coupled i-f amplifier having
heat-dissipating metal back plate and individual metal rube envelopes for conducting
tube heat to the plate.

Table II) Resistances of Etched Copper-Foil Conductors.
By S. F. Danko and S. J. Lanzalotti Signal Corps Engineering Laboratories
Fort Monmouth, New Jersey
The system of miniature circuit assembly to be described was evolved as a result
of several Signal Corps study programs, aimed at providing relief from the production,
performance and maintenance problems attendant on highly compact sub-miniature equipment
designs. The system designated as Auto-Sembly borrows the very convenient prefabricated
conductor pattern of printed circuits, and permits rapid and effective electrical
combination of this pattern with conventional quality components by a one-shot solder
dip process. The elements of Auto-Sembly are : (1) Formation of the conductor pattern;
(2) selection of components; (3) rapid assembly; (4) packaging.
Of the many techniques of metallization extant today, the etching of copper-faced
laminates (electrolytic copper foil bonded to an insulating base) provides one of
the most convenient means of pattern fabrication. In this subtractive process, a
resist image of the desired conductor pattern is printed or otherwise delineated
on the copper foil surface and the laminate then exposed to an etchant. The resist
material protects the metal against the action of the etchant during the short etching
period. The Signal Corps Laboratories demonstrated early in 1949, in collaboration
with the Etched Products Corp. of Long Island, that the commercial offset presses
of the etched nameplate industry could be readily adapted to the deposition of such
resists on commercially available foil laminates for subsequent etching.
The photo-etch technique of the graphic arts industry was equally well adapted
to such resist fabrications, particularly where higher orders of definitions or
reproducibility were desired. Several other metallizing techniques, including the
Mallory pressed powder technique and the Franklin Air-Loop stamping process, are
also compatible with the Auto-Sembly system since they yield high-conductivity patterns
which are amenable to component assembly by solder dipping.
It is the intention of this presentation to emphasize the etched-foil technique
of preparing a conductor pattern, inasmuch as this process lends itself excellently
to pattern fabrication by the laboratory designer for prototype model constructions.
The choice of a process for forming the pattern for production depends on such factors
as the detail required in the pattern, quantities involved, tooling costs, production
rate and delivery time.
Laminates
The physical characteristics of the commercially available copper-faced laminates
which are of prime interest for Auto-Sembly include bond strength of the foil to
the laminate, compatibility of this bond with the temperature shock conditions which
it will experience during solder dipping, dielectric constant, power factor, arc
resistance and moisture absorption. Table I lists in a general way some of this
physical data for comparison purposes, and Fig. 1 shows the relation of losses to
frequency for several of these laminates. It should be noted that these loss curves
apply where the base material is used as the total dielectric, between metallized
faces on opposite sides of the material. In the usual application, where capacitances
between adjacent lines are of concern, the losses are substantially lower than indicated
since the dielectric is part air. The laminates are also available with copper on
both sides to permit fabrication of aligned patterns on both faces. Most common
thicknesses of copper are 0.00135", 0.003" and 0.005".
Resists
Within the design laboratory, screening of the resist is perhaps the simplest
and most convenient method of printing the pattern prior to etching. The screens
themselves may be prepared by any of the many commercial screening organizations
or may be prepared within the laboratory without too much art or effort. For most
general line work for conductors, a screen mesh of about 150 per inch is adequate.
Satisfactory resists for screening are many, but synthetic screening enamels
available from the art supply houses have been particularly useful in this application.
An example is the Synthetic Screen Enamel, series 1500, any color, obtainable from
the Colonial Process Supply Co., New York City. Resists made by dissolving asphaltum
in an appropriate vehicle are also convenient, but care must be taken to get the
proper screening consistency. The synthetic enamel resists require approximately
8 hours to dry (overnight, or may be oven dried in a few hours).
The foil laminates with the resist patterns may be etched in a rocking tray or
may be mounted copper face down about one-half inch over the surface of the etchant,
which can then be agitated by bubbling air violently through the solution. The recommended
etchant for copper is a 50-percent solution of ferric chloride. This will etch through
a 1.35-mil foil in about 5 to 7 minutes depending on the freshness and temperature
of the bath. The patterns are then washed in running water, following which the
enamel resist can be removed by use of a thinner or by light abrasion. Commercially
these patterns would then be processed through a die stamping operation to provide
the necessary holes through the pattern at each termination point. In the laboratory,
of course, these perforations would be drilled or punched.
Conductor Characteristics
The thinner copper foils have more than adequate conductivity for general miniature
circuit applications, as indicated in Table II. A 1.35-mil-thick conductor 1/32-inch
wide on a representative 3 x 2-inch phenolic plate will carry over 3.5 amperes continuously
with a 40-degree C maximum temperature rise of the conductor. A similar 3-mil-thick
conductor under the same conditions will carry over 5 amperes. A studied effort
has been made to discourage use of such ratings as fusing currents, peak current
capacity and similar short-time ratings which do not provide useful information
for a designer's guidance.
For general conductor applications a line width of about 1/32-inch is recommended,
although widths down to 1/64-inch are dipped consistently. Experience to date indicates
that an area of metal equivalent to about 1/16-inch-diameter circle at each junction
point is desirable since a well-formed and substantial fillet of solder will then
be built up. Spacing of lines, in general, should be kept at least at 1/32-inch
unless otherwise demanded by pattern layout.
On phenolic surfaces, the peak flash-over voltages at room ambient conditions
with no coating protection over the h-inch pattern spacings were about 1,800 v.
This es-inch spacing has been used consistently on 300-v d-c circuits, with no failures
recorded. In this respect, the desirable arc resistance features of some of the
laminates are strong points in their favor. With this spacing, insulation resistances
well over 100,000 megohms under ambient room conditions are measured between 3-inch-
long copper lines on phenolic with no protective finishes applied.
The distributed capacitance between lines is significant and cannot be ignored
at the higher frequencies. On XXXP phenolic, this capacitance is of the order of
1 µµf per inch for 22-inch spacing and 0.7 µµf per inch for 1/32-inch spacing. These
values will be lower for the lower dielectric constant materials. Proper pattern
layout will allow use of very short sections of r-f conductors, and it has been
convenient at times to run short ground lines between two critical conductors to
reduce this electrostatic coupling to a still lower figure.
Although the inherent power factor of such materials as phenolic is fairly high,
the effective power factor is considerably better inasmuch as the dielectric of
the distributed capacitance is part air and part insulating material. As a generality,
this pattern capacitance can be said to be comparable in magnitude to that which
may be encountered in conventionally wired compact assemblies, but with the advantageous
feature of being identical from pattern to pattern.
The commercial offset press process can yield line work of the order of 8 to
10 mils in width as a matter of routine production. The photo-etch technique yields
conductor widths down to about 4 mils without premium charges. These higher definitions
are useful in delineating the precise geometry required of spiral-formed coils such
as have been used in television tuners and high-frequency i-f coil patterns.

One-watt audio amplifier with portion of metal heat-dissipating
container cut away to show use of folded circuit. Components are Auto-Sembled on
flexible Teflon chassis that is rolled up and inserted in container, then cast in
resin. Subminiature tubes fit into machined holes in solid metal end of container.
It is recommended that the finished copper patterns be silver-surfaced by dip
plating (which yields a satisfactory flash coat) or by direct plating to eliminate
oxidization of the metal on long storage with the subsequently increased difficulties
of cleaning. The commercial etching houses will supply such surfacing as a matter
of normal production processing.
Copper has been mentioned exclusively as the conductor material because of commercial
availability of the copper-surfaced laminate. However, some of the etching sources
which do their own laminating have prepared patterns of brass, silver, iron, aluminum,
bronze and even spring -tempered steel for special purposes. Some of these metals
have proven particularly useful in delineating patterns for switches. It should
be mentioned, too, that these laminators-etchers can supply embossed, flush or subsurfaced
patterns for special purposes or provide upset metal nodules on the patterns where
required for switch contact points.
Components
Auto-Sembly requires that the components have stiff protruding terminations,
preferably of a radial type, such that the component can be conveniently inserted
into its designated place on the insulated side of the chassis. Resistors, capacitors
or other components having axial leads can have these leads cut and shaped by jigging
machines built for this purpose. The production arrangement can be such as to have
the operator hold the conventional component momentarily in the jig for shaping
and then in the next motion insert it into place on the pattern. The alternate proposition
would be to supply the operator with pre-jigged components. Components where stiff
protruding terminations are desired include termination devices such as sockets,
connectors and receptacles. Current Signal Corps developments aim to provide such
electro-mechanical devices that are particularly adapted to Auto-Sembly or other
card-type systems.
Most conventional components can be readily adapted to Auto-Sembly mountings.
The use of conventional components is considered a desirable and realistic approach
in this miniaturization technique. The designer has available for his choice not
only the variety of components but also the full range of tolerances, electrical
characteristics and physical sizes in the established quality lines of JAN or commercial
components. There are no special skills imposed on the assembler of the equipment
such as would be required if he were to deposit or print his own resistors or capacitors.
The fabrication of such deposited components is still a highly specialized art.
Where economic or performance advantages can be realized in any fabrication through
the use of these printed circuit aggregates, then such groupings of deposited components
(such as Couplates, Bulplates and multi- value capacitors) can be treated like any
other component for Auto-Sembly.
Assembly
The use of the one-shot solder-dip technique has been particularly convenient
in the fabrication of highly miniaturized assemblies. In this operation the insulating
base, with the fluxed pattern on the underside and the components mounted on the
topside, is momentarily dipped in a eutectic solder bath (63 percent tin, 37 percent
lead) maintained at about 450 F. The period of dip recommended is of the order of
two or three seconds, but this time may be increased if large areas of copper are
left on the pattern for shield purposes or as heat radiation surfaces. Periods of
dip as high as ten seconds have been made without delamination or deleterious effects
on such base materials as phenolic, Teflon or silicone.
Mobilization Advantages
SAVES LABOR by eliminating manual wiring, which ordinarily requires
more man-hours than any other step in electronic equipment manufacture.
MINIMIZES REJECTS because etched wiring is absolutely uniform
from chassis to chassis.
ELIMINATES UNSOLDERED JOINTS because all joints ore made simultaneously
in one solder-dip operation
REDUCES INSPECTION TIME because mechanization reduces probability
of errors practically to zero.
SPEEDS ASSEMBLY TIME because leads of components are simply pushed
into holes, with no hook or wrap-around joints.
PERMITS GREATER MINIATURIZATION, because etched wiring takes
practically no space and lends itself to stacking of chassis layers.
IMPROVES RELIABILITY, because Auto-Sembly practically eliminates
short-circuits between connections and lead.
The success of the solder dip procedure is particularly dependent on the flux
used just prior to solder dipping. The following formulation has been found successful:
1 part Glyco Wax No. S932 made by the Glyco Corp., Brooklyn, N. Y.; 1 part Kester
No. 1015 (activated rosin in alcohol flux) made by the Kester Solder Co., Newark,
N. J.; 1 part toluene (more toluene may be added if a thinner consistency is desired).
The bath should be kept warm during use (about 110 F). The flux itself may be applied
by dipping the pattern side momentarily in the flux or by brushing the flux over
the pattern.
It is important that the pattern be removed from the surface of the solder bath
with a sidewise lifting motion. This technique yields a soldered pattern with well-formed
fillets at each termination point and a more or less hemispherical cross- section
of solder on the conductor lines. The pick-up of solder on the conductor lines is
extraneous and incidental to the process but it does add to the total conductivity
of the conductors. One manufacturer on a production line basis has evolved a variation
of this technique wherein his solder dip procedure deposits mechanized solder only
at the termination points, a desirable process from the point of view of solder
economy.
Packaging
Packaging includes ruggedization, moisture protection, adequate heat transfer
and provision of connective components such as may be required for plug-in use.
Use of right-angled connectors provides a convenient means of integrating a connector
quickly to the pattern since such a connector is treated as any other component
in the course of the assembly operation.
Although stiff laminates have been discussed up to now, flexible laminates have
been used as the chassis for the pattern in making folding circuits. Assemblies
on thin sheet Teflon glass laminates and on silicone rubber (thicknesses of 3 to
10 mils) have been Auto-Sembled and then folded and inserted into capsules.
Conclusions
The complete and detailed coverage of all aspects of the Auto-Sembly system have
not been presented here because of the voluminous nature of an exhaustive treatment
of the subject. It can be shown, for example, that sections of Auto-Sembly circuitry
can be decked by providing completed solder-dipped Auto-Sembled sections with stiff
swaged-on protruding connectors which can be inserted into place on another deck
and then solder-dipped into place. Crossovers can be made by eyeleting and subsequent
spot-soldering on double-faced laminates, or by use of staple-shaped wires as components.
The information as presented has been intended to show some of the more basic
concepts and techniques of Auto-Sembly and the major considerations which govern
its current applications in service and commercial equipment application. The use
of the etched pattern and the Auto-Sembly system of integra- tion both provide effective
tools which are not necessarily limited to electronic circuit fabrication. These
patterns, for example, are used in the preparation of heaters, Faraday shields,
switching devices, and in one instance even for forming low value bypass capacitors.
Auto-Sembly is being used in new military equipment designs and is currently applied
commercially to repetitive types of circuits such as are used in counters. The extrapolation
of Auto-Sembly to other applications is dependent almost entirely on the imagination
of designers familiar with the capabilities of these tools.
Posted November 8, 2022
|