August 1965 Electronics World
Table
of Contents
Wax nostalgic about and learn from the history of early electronics. See articles
from
Electronics World, published May 1959
- December 1971. All copyrights hereby acknowledged.
|
Arthur Steele is probably
enjoying retirement from Littelfuse
(still in business today) by now. In 1965 he had an
article published offering guidelines on how to select the proper type fuse for
protecting the circuit at hand. The correct choice is seldom a simple matter of
adding a margin of some amount onto the known maximum current draw, especially if
you are designing for a commercial or defense electronics project. Applied voltage,
expected current
surges, operational temperature and mechanical
stress (vibration & shock, etc.), applicable design
regulations (UL, Mil-Spec, etc.), serviceability,
and available space are among the factors that need consideration. Do you need a
fast-blow, medium-blow, or slow-blow fuse for that circuit? You'll have a good understanding
after reading Mr. Steele's piece. The automotive blade fuse type
(thumbnail to left) so common today was not around
at the time; they first came on the scene in the 1980s. See also
Fuses for Electronics in the July 1972 issue of Popular Electronics.
Selecting the Proper Fuse
By Arthur J. Steele, Staff Engineer, Littelfuse,
Inc.
Important factors to consider include physical size, amperage, voltage, type,
ambient temperature, and special characteristics. A number of important rules for
proper fusing are included.
A fuse is an intentionally weakened part of an electrical or electronic circuit.
Its purpose-is to protect the other elements of the circuit from a possibly damaging
overload. If it is to perform its function of protection properly, it must be thoughtfully,
selected and installed or mounted. Fuses are used to protect many different types
of circuits. In some instances we are trying to protect only the wiring and prevent
a fire. In other instances, we may be protecting a very sensitive meter or an electronic
component in a television set.
Fuses are generally a glass-bodied cartridge with nickel-plated brass caps. High-amperage
fuses are made of a punched zinc alloy element. Low-amperage fuses are made with
a filament wire of many materials from copper to platinum and many alloys to accomplish
the desired result.
Rules of Fusing

Glass and ceramic cartridge fuses. From left: 3AG medium-lag
type; slow-blow fuse; 3AB ceramic anti-vibration fuse with arc-quenching filler;
8AG low-current instrument fuse; and 4AG low-voltage medium-lag fuse developed for
aircraft use.

Fig. 1. Characteristics of fast-, medium-, and slow-blow
fuses.
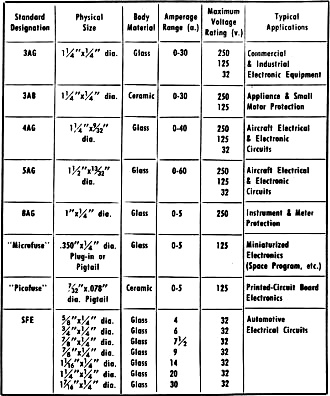
Table 1. Listing of fuses commonly used in electronic equipment.
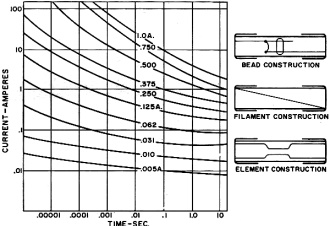
Fig. 2. Typical family of characteristic curves for 8AG
high-speed instrument fuses of various current ratings. Most of these fuses are
low-current devices with bead or filament construction.

This super-small, fast-acting ceramic cartridge fuse will almost
fit through the eye of a needle. Fuse is only 7/32" long and 0.078" in diameter
and is available at up to 5 amps.
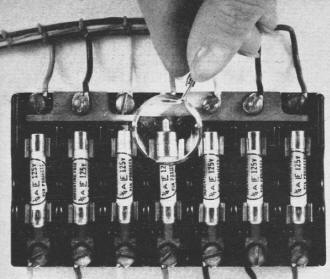
A group of medium-lag indicating fuses is shown. When this fuse
blows, the silver-plated indicating pin extends from the end of the fuse. This serves
as a visual indicator. The pin can also be used to actuate an audible alarm circuit
as well.
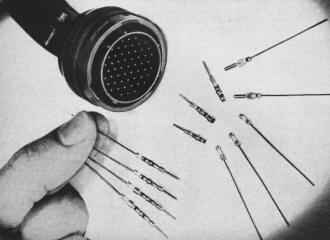
Subminiature fuses may be assembled into cylindrical pin contacts
which are then inserted into military and industrial connectors.

Fig. 3. Characteristics of slow-blow fuses for motor protection.
The first question that must be answered is, "What am I trying to protect?" Is
it the wiring of a house? the wiring of an electronic device in industry? the wiring
of a very sensitive mechanism to be used in our space program? In each case, am
I trying to protect against a fire hazard? or am I trying to protect a piece of
equipment? a very sensitive metering device? an expensive component? or eliminate
shock hazard to personnel? There is a definite series of questions that you should
ask yourself when deciding on a fuse. Ask yourself the following questions:
1. What is the normal operating current?
2. What is the abnormal current at which the fuse is required
to open the circuit?
3. What are the minimum and maximum times during which abnormal
current is permitted?
4. What voltage is applied to the fuse?
5. What is the normal ambient temperature at the fuse location?
6. Are there pulse characteristics involved in the circuit?
7. What are the applicable commercial specifications?
8. Are there any applicable government specifications?
9. Are there other requirements special to this application
(mechanical or electrical characteristics) beyond the normal requirements of a commercial
fuse?
10. What is the physical size desired?
Types of Fuses Used
The number and types of fuses and fuse mountings required by the electronics
industry have developed over the past 25 years in about the same proportion as those
of resistors and capacitors. In the same way, too, the pressure from engineers has
been to make fuses smaller and better. By far the greatest number of fuses used
in electronic components and circuit protection are glass-enclosed, although ceramic
is used for the higher current, 250-volt Underwriters' Laboratory listed fuses.
The common fuse families are listed in Table 1. The most popular fuses, their
sizes, and maximum ratings are given, along with their standard industry type designation.
Readers will be interested to note that there is no logical or rational relationship
between the recognized "AG" designation and the physical size of the fuse. It has
grown rather haphazardly over the past 40 years, starting with the automotive industry.
1AG was the first "automotive glass" fuse; 2AG was next (no longer used, dropped
in an effort to standardize); 3AG was next, etc.
As the industry grew, additional sizes were necessary and they did not necessarily
fall within the physical size order. In addition, the SAE (Society of Automotive
Engineers) established a specification in an effort to try to prevent over-fusing
by making the fuses non-interchangeable. As the amperage rating was increased, the
physical length of the fuses was increased, thus preventing over-fusing. This approach,
however, has not been too practical due to the limited number of amperage ratings
available.
In general, then, the "AG" designations only classify the fuse as to the specific
physical size of the envelope in which the fuse is placed.
The need for smaller and better fuses has led to the development of such fuses
as the "Microfuse" and "Picofuse." The "Microfuse" is being used in the Gemini space
program. It is small, accurate, and reliable, and is produced in either plug-in
or pigtail versions. The "Picofuse" is a pigtail-type fuse with either radial or
axial leads. This fuse is the smallest of protectors - accurate and fast-acting.
It may be used where space and weight are at a premium and where mechanical and
electrical requirements are high.
Fuse Characteristics
Fuses are the safety valves of electrical circuits, therefore it is important
that they operate or "blow" before damage occurs in either the equipment or the
wiring being protected. Conversely, we do not want to have nuisance blowing. Thus,
fuses must not blow too easily and cause open circuits when the equipment is operating
normally.
It becomes obvious that time and current are the controlling factors in the function
of a fuse. There is a time and current relationship at which the circuit will operate
satisfactorily and cause no damage to equipment or wiring. There is also a time
and current relationship at which the equipment will be damaged. In other words,
the time-current characteristics of the fuse must conform to the time-damage characteristics
of the equipment.
There are three basic types of fuse characteristics for different types of applications.
Fast-blowing fuses are used for instrument protection where fast action is necessary
in order to protect the equipment. Medium-blowing fuses are used for general applications.
Slow-blowing fuses are used for applications where a time lag is desirable (see
Fig. 1).
Fast-acting fuses are designed to carry 100% of current rating and blow rapidly
at very slight percentages of overload. For example, they will open the circuit
at a 200% overload within a maximum of 5 seconds. The greater the overload, the
more rapidly the circuit opens. There is very little mass in the filament used,
therefore the reaction can take place very quickly under short-circuit conditions.
This filament is generally made of silver, platinum, or other precious metal alloys.
These fuses are manufactured with wire diameters as low as 0.000020". Obviously
this filament will open the circuit under adverse conditions before any damage can
be done in other parts of the circuit. Typical examples of the fast-acting fuses
are the 8AG instrument fuses (see Fig. 2), "Microfuses," and "Picofuses."
There are three basic constructions of these fast-acting fuses. One, the bead-type
construction, uses a small onyx bead holding two heavy wires, across which is placed
a fine filament. The second is a filament-type construction employing a diagonal
lineup to insure the constant blowing characteristics of the fuse; and third, the
element construction for heavy amperage fuses in this design. By observing the characteristic
curves, it will be noted that as the amperage rating increases there is an inherent
lag; automatically built-in, due to the increase in mass of the fusible link.
Medium-Lag & Slow-Blow Fuses
Medium-lag fuses are by far the most widely used. They are used in automotive,
commercial, and industrial electronic equipment, as well as in appliances. These
fuses are designed to protect a non-critical device, wiring, or equipment at minimum
cost. In general, they are designed to carry 110% of rated current for a minimum
of four hours. Circuits will be protected if an overload of 135% of rating is placed
on the fuse; it will open in less than one hour. If an overload of 200% of rating
is placed on the circuit, the fuse will open the circuit in a maximum of 30 seconds.
Notice that the action of these fuses is not as rapid as the fast-acting fuse. However,
they are perfectly satisfactory in the majority of general applications for fuse
protection. All SFE fuses fall into this category, as do many of the 3AG and 3AB
fuses.
The slow-blow fuse is one that has a time-lag characteristic. Many circuits or
pieces of equipment have a built-in pulse characteristic which is normal for the
operation of this equipment. The starting of a motor, for example, produces the
pulse characteristic referred to. Until the motor is up to speed, current far higher
than the normal running current flows in the circuit. This is normal operation for
this circuit, so we do not want the fuse or protector to open the circuit during
these conditions. Therefore, a fuse must be designed with sufficient mass or time
lag to prevent nuisance blowing. In some highly inductive or capacitive electronic
circuits, this same characteristic is required.
In the design of fast-acting fuses, we want to have a minimum amount of mass
in order to cause the fuse to open the circuit as quickly as possible. For the slow-blow
characteristic, the reverse is true. We want a period of delay, therefore additional
mass of one type or another is added to the fusible link, thus causing a delay.
This can be done by using a relatively large mass of low-melting point alloy placed
near the heat-generating source. The fuse, being a thermal device, requires a certain
amount of time for the current passing through a certain resistance to cause a reaction.
It requires a certain amount of time for the current passing through the heat-generating
source, or the resistance of the fuse, to bring the temperature of the low-melting
point alloy to the point where it becomes liquid, triggering the mechanical action
of a tensioning spring, and opening the circuit. The time that is required for this
reaction is called the slow-blow or lag characteristic of the fuse.
The low-melting alloys are made up of tin, lead, bismuth, and small quantities
of other materials to control the desired melting point. The heat-generating source
takes many forms, depending on the amperage rating of the fuse. In some instances
a small carbon or wirewound resistor is added, or the resistance of a coil spring
becomes the heat-generating source.
In most applications, the time-lag characteristic is desirable only in a limited
range of operating currents. The current values in excess of this limited range
require the fast action. therefore, slow-blow fuses are designed to carry 110% of
rating for a minimum of four hours and open the circuit at 135% of rating within
one hour, have a minimum of 5-second delay at 200% of rating, and open the circuit
within 2 minutes.
For overloads in excess of 700%, a fusible link is placed in series with the
slow-blow fuse so that fast action is obtained in opening the circuit when an overload
of this nature is encountered. Three types of characteristics are actually available
in the slow-blow type fuse. First, a long life at the normal operating characteristic;
second, a time delay to prevent nuisance blowing under slight overloads; and third,
rapid action under short-circuit or high overload conditions. This type of fuse
is used in TV horizontal sweep circuits, power supplies, motor circuits, etc. See
Fig. 3.
Fuse Mounting
There are many different ways of mounting fuses. The least expensive is the addition
of a pigtail-or wire-to the ends of the fuse, which can then be soldered directly
into the circuit. The second method, and one which is very commonly used, is the
open-clip-type mounting where the fuse is supported by metal fuse clips and the
circuitry is either wired or attached by screw terminals or solder lugs to the fuse
clip. The third refinement is the fuse-extractor post, which is generally panel-mounted,
giving access to the fuse from either the front or back panel without danger of
shock hazard to the operator. In automotive or low-voltage applications, another
method of mounting is offered in the fuse retainer, or in-line type mounting.
When many fuses are used, it is desirable to have some indication of which fuse
has blown; therefore, indicating fuse-extractor posts are available. In this type,
a lamp in the transparent knob of the fuse post lights up at the time of fuse failure,
indicating which circuit has the blown fuse. When the fuse is replaced with a good
fuse, the light is no longer energized. There are also available special types of
fuses with built-in indicators to show when a fuse has blown.
There are some specialized holders for specific applications, for example, the
limited-current fuses and fuse holders used for TV sets. These limited-current fuses
are made with a pair of tabs on one cap, which are indexed with a pair of slots
in the head of the fuse holder. As the amperage rating is increased, the tab width
is increased, thus making it impractical to use a higher rating of fuse.
Common Fusing Errors
There are some common fusing errors in the use of fuses which create problems
for the user and, in some instances, result in damaged equipment. One of the most
common errors is over-fusing. A piece of equipment may be designed to use a certain
amperage fuse - which gives adequate protection. Because of overloading, the fuse
blows occasionally and when the fuse is replaced, the equipment seems to work all
right. Because of this, the obvious conclusion to the layman is, "Put in a larger
fuse and everything will be OK." A larger fuse is installed and suddenly there is
a cloud of smoke due to the continuing overload and the use of a fuse that is not
capable of opening the circuit because it is overrated for that particular application.
Always replace a blown fuse with the same rating fuse that was originally designed
into the equipment. There have been many instances where 1/4-amp. fuses have been
replaced by 20-amp. units in order to prevent nuisance blowing. Obviously, over
a period of time this can only lead to ultimate failure of the equipment.
Another common fusing error is using the wrong type of fuse in a piece of equipment.
For example, a piece of equipment that has a high inrush surge should not use a
medium- or fast-blowing fuse. In this type of application, a slow-blow fuse should
be used, thus preventing nuisance blowing and the possibility of up rating or over-fusing.
On the other hand, for the protection of a delicate instrument or an instrument
circuit, we want a fuse that will open the circuit as quickly as possible in order
to prevent damage. In this case, the use of a medium- or slow-blow fuse would not
be correct. An instrument fuse, or fast-blowing fuse would be the correct choice.
Remember, use the right type of fuse for your particular application.

These slow-blow fuses have different lengths and different widths
of bayonet locking tabs on the fuse caps. The fuse post accepts only one type so
that over-fusing is prevented.
The use of a fuse with the wrong voltage rating is also a common fusing error.
The voltage rating of a fuse is the maximum voltage it will break without arcing
or bursting. (This is assumed to be in a direct-current system with a 10,000 ampere
capacity power supply, unless otherwise indicated.) In other words, 32-volt fuses
should not be used in 250-volt circuits. This can be dangerous to the user as well
as to the equipment in which it is installed. All voltage ratings on fuses are maximum
voltages; fuses may be used up to and including their voltage rating.
The ambient temperature is a contributing factor in the opening of a fuse. One
of the common errors in fusing is a complete disregard of the temperature in which
the fuse is required to operate. We have stated that the fuse is actually a thermal
device. It operates by virtue of the heat dissipated in the fuse element. Therefore,
an increase in ambient temperature can also cause de-rating of the fuse. Conversely,
a decrease in ambient temperature can also cause an increase in rating in the fuse.
Thus, when temperatures other than normal room temperature are encountered, they
should be taken into account in selecting appropriate fuses.
Other minor considerations often overlooked yet responsible for fusing errors
include pulse fatigue, vibration, shock, and exceptional atmospheric conditions.
All of these conditions should be considered at the time the equipment is designed
and the fuse application determined. This is another good reason for replacing fuses
that have blown in service with the same type of fuse that was in the original installation.
In summary, when choosing a fuse for your particular application, select the
proper unit by carefully considering the following: 1. size, 2. amperage, 3. voltage,
4. type, 5. ambient temperature, and 6. special characteristics.
The selection of proper fuses can prevent nuisance blowing, fire hazard, and
danger to personnel.
Posted November 8, 2023 (updated from original post on 6/13/2015)
|