August 1956 Popular Electronics
Table of Contents
Wax nostalgic about and learn from the history of early electronics. See articles
from
Popular Electronics,
published October 1954 - April 1985. All copyrights are hereby acknowledged.
|
In part one of a two-part
article, Popular Electronics magazine presents some of the inner workings
of what at the time was a fledgling industry - printed circuit board manufacturing.
In 1956, when this piece appeared, a large percentage of electronics assemblies
were still being wired in a point-to-point manner where resistors, capacitors, inductors,
tubes, and cables were soldered directly to terminals either on special blocks or
on tube sockets. The process was heavily labor intensive and prone to miswirings.
High volume production was nearly impossible prior to printed wiring boards (PWBs).
Bell Telephone Labs was an early adopter and driver of the technology. A good example
of an early telephone PWB can be seen in the 1970s vintage
Snoopy telephone that I reconditioned a while back. Note the rat's
nest of wires going to the network terminal block. Here is
Part 2.
Check out "How to Etch Professional Printed Circuit Boards" in the March
1966 Popular Electronics.
"Printed Wiring" Techniques for the Experimenter
By Louis E. Garner, Jr.
Part I of two-part series discusses methods of printed wiring and tells how to
make an etched circuit board
Courtesy of Bell Telephone Labs.
Radio receiver "wired" without hookup wire! An audio amplifier, assembled without
terminal strips! A television receiver with hundreds of soldered connections ...
but all made without a soldering iron!
Far-fetched? No, All of these production miracles may occur as a matter of course
when a manufacturer substitutes "printed" wiring methods for conventional hand wiring,
Since the elimination of hand wiring can cut labor production costs as much as 50%,
manufacturers have a sound economic reason for using such methods.
But the savings in labor costs is not the only reason for going to printed wiring.
The finished equipment may be more compact, work better, and require fewer adjustments.
Finally, since every unit is wired exactly alike, wiring errors are virtually eliminated,
"rejects" are minimized, and inspection time and costs are reduced.
Methods of Printed Wiring. The general term "printed wiring" is used to describe
any electrical or conductive pattern reproduced on an insulating base, although
technically the term applies only to wiring and circuits reproduced with the aid
of printing techniques ... that is, using conductive inks printed in the desired
pattern. Commercially, printed wiring may be of two general forms - "deposit" and
"stripped."

In making up a printed·-circuit layout, you start with a schematic
wiring diagram of the project you plan to assemble, redrawing it until you have
eliminated all circuit wiring crossovers. See text for more details.

Typical etched circuit layout on cross-section paper. Drawing
should be made to full-size scale.

Clean the copper-clad phenolic wiring board of dirt and tarnish
prior to applying the resist.
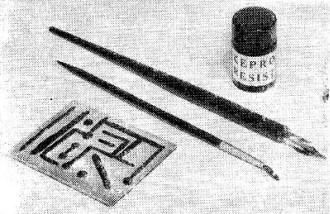
Ink resist is applied with brush and pen. Only those parts covered
will remain after etching.

Scotch electrical tape may be used as a tape resist. Circles
are cut out with a paper punch.

If a "deposit" method is used, the conductive pattern is applied to the insulating
base plate. Typical "deposit" methods include printing with metallic inks, spraying
liquid metal onto the base through a stencil, and pressing a metallic foil pattern
into a plastic base, using a heated die.
Where a "stripping" method is used, the insulated base is covered with the conducting
material. The desired pattern is applied to the surface, and the excess conductor
"stripped" away. The more popular "stripping" techniques include etching and embossing.
Use of printed wiring methods offers advantages to the home experimenter, student,
or gadgeteer making up a single circuit as well as to the manufacturer producing
thousands of units. When reasonable skill is acquired through practice, it is often
possible to layout, produce and assemble a piece of equipment using printed wiring
in less time than it takes to make up the same circuit using conventional wiring
techniques ... and with the final equipment much more "professional" in appearance,
more compact, and likely to work better.
With the advantages to the experimenter in mind, several manufacturers are offering
printed-circuit kits. These kits include all the materials necessary to make up
etched circuit boards. Basic printed wiring techniques have been described briefly
in past issues of Pop'tronics in regard to specific projects. See H. J. Carter's,
"Making an Etched Preamp" (November, 1955, p. 87), and Paul F. Runge's "Printed
Circuitry for R/C" (August, 1955, p. 74). But now we'll discuss these techniques
in detail and show how you can apply printed wiring methods to virtually any project
that you wish to assemble.
Of the various printed wiring techniques used industrially, the techniques of
"etching" and "painting" are best suited to home use. Of the two, etching is by
far the most popular and is, in fact, the most widely used commercial technique.
The majority of printed-circuit kits utilize etching techniques.
Making Etched Circuits. The basic. steps in producing an etched wiring board
and assembling a circuit are illustrated in Fig. 1 (p. 62). The raw material
is a laminated ,board consisting of an insulating base with a layer of metal foil
bonded to its surface. The foil may be on either one or both sides. In most work,
a copper-foil clad laminated paper-base phenolic Is used.
You can make up your own etched circuit boards by following these essential steps
- plus the additional steps of making up the original circuit pattern layout and
transferring the layout to the board. Follow the procedure detailed below:
Step 1 - Making a Layout. Start with the schematic wiring diagram of the project
you plan to assemble. Redraw the schematic one or more times, trying to eliminate
all circuit wiring crossovers. When you have a tentative circuit, gather the components
you plan to use and make a full-size scale drawing of the final circuit. Locate
components where they will serve to bypass conductor crossovers which are not easily
eliminated. Individual leads or "wires" should have a thickness of at least 1/32",
with the spacing between adjacent conductors not less than 1/32". Thicker leads
may be used if desired, and you may find it easier to work with 1/16"- or even 1/8"-wide
conductors on the first few boards you make up.
Where components are to be mounted or leads attached to the board, draw small
circles. Entire patches of foil conductor may be used for shielding, although it
is generally best to "break up" solid areas with diagonal bars. The spacing between
adjacent bars may approximate or be slightly greater than the width of the bars.
Where 90° turns are made, the conductor may follow a smooth curve or make a
sharp bend, as preferred. Where eyelets are to be used, plan on holes large enough
to accommodate them. Use slightly smaller holes when leads are to be attached directly
to the copper foil.
In general, component and wiring leads can be soldered directly to the copper
foil for permanent connections, but if the leads may be removed often, plan on using
copper or brass eyelets at such points. Space component mounting holes for the actual
parts you plan to use. If the components are to be mounted by their leads (resistors,
capacitors, and small coils are generally mounted in this fashion), space the mounting
holes with the thought of using a gradual bend in the component leads instead of
a sharp bend close to the body ... sharp bends may cause the leads to break off
or can place an undue strain on the component. You will find that cross-section
(graph) paper is useful for making up the scale wiring layout.
A "typical" printed wiring layout is illustrated in Fig. 2. This layout
has been designed to illustrate important points to remember when making up your
own layouts and it does not represent a specific circuit.
Upon completing a circuit wiring layout, check and double-check for errors. While
still in the layout stage, an error may be corrected simply by erasing and redrawing
the layout ... but once the board is etched, it may be necessary to make up an entire
new board to correct mistakes.
Step 2 - Preparing the Board. The copper-clad phenolic board
and other materials
you'll need may be purchased individually or in "kits." (See list of suppliers on
page 62.) At the beginning, however, you'll find it best to purchase a complete
"kit" of materials. Once you've gained a little experience in making up circuit
boards, you can purchase individual items in the quantities needed.
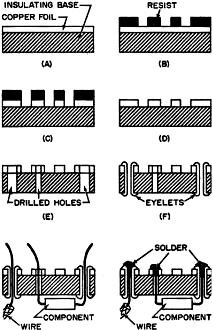
Fig. 1 - In the commercial production of etched circuit boards,
the plain metal clad board shown at (A) is covered with a special material which
resists chemical action. This "resist" is applied in the pattern of the desired
final circuit, as shown at (B), using photographic, plating, spraying, stenciling,
or printing techniques. With the resist applied, the foil-clad board is placed in
a chemical etchant which attacks and eats (etches) away all unprotected metal, leaving
only the foil pattern protected by the resist (C). After that, the resist is removed,
exposing the bare metal foil (D). Machining is next (E), with mounting and wiring
holes drilled or punched at appropriate places in the board. Metal eyelets, if used,
are now mounted in the board (F). With step (F), the wiring board itself is completed.
To complete the circuit, electrical components are mounted on the back of the board
by passing their leads through appropriate holes in the board (G). Finally, the
board is soldered and excess lead lengths cut off, resulting in the completed circuit
shown at (H). In production work, the entire board is generally soldered in one
operation by dipping it into a "pot" of solder - with the operation called, appropriately,
"dip soldering." Thus, hundreds of soldered connections may be made at one time
without a soldering iron!
Depending on the circuit layout, use either single-sided (single-clad) or double-clad
boards. But until you gain experience, you'll find it best to stick to simple layouts
and single-clad board.
Cut a piece of the copper-clad board to fit your circuit layout, using a fine-toothed
hacksaw, a jigsaw, or a scroll saw. Cut from the copper side, and back up the thin
phenolic board with a piece of hardboard or plywood. If any large holes or cutouts
are needed (for tube sockets, for example), they should be cut at this time. Use
a hole saw or "flying bar" cutter for cutting large round holes ... not a conventional
chassis punch, which may crack the board. Only the large holes and cutouts are made
at this time ... smaller holes are drilled after the board is etched.
With the board cut to size and rough machine work completed, clean the copper
surface of dirt and tarnish, and roughen it slightly to permit the etchant to get
a better "bite" on the foil. You can do this by scrubbing the surface with a stiff
brush dipped in powdered pumice stone (check your local hardware dealer) or, if
pumice stone is unavailable, by using an abrasive household cleanser. Sprinkle the
household cleanser lightly on the foil and scour vigorously with a slightly dampened
cloth. With the surface properly prepared, the copper should be bright and shiny,
and should have many small scratches ... visible when the foil is examined through
a small magnifying glass. Then you should rinse and dry the prepared board.
Step 3 - Transferring Layout. First, obtain a few sheets of "pencil" carbon paper
from your local stationer or office supply store. Cut a piece to fit your circuit
board and attach the carbon paper and your scale wiring layout to the board with
Scotch tape. Make sure the layout cannot shift its position. Finally, using a moderately
hard pencil, trace the layout onto the copper foil.
Locate small mounting holes by pricking the copper right through the layout and
tracing carbon, using a small center punch or a sharp scribe. Use hand pressure
or a very light hammer tap when locating these holes to avoid cracking the board.
Back up the board with a solid piece of hardboard or wood. And double-check your
tracing before removing the layout sheet and carbon paper.
Step 4 - Applying the Resist. With the circuit layout transferred to the copper-clad
board, the acid "resist" may be applied. For experimental "single-shot" circuits,
two types of resist are popular: (1) ink resist and (2) tape resist.
Ink resist is an asphalt-based acid-resistant paint or ink. It is supplied as
a part of most printed-circuit kits but is also available from many art supply houses.
Apply ink resist to the copper foil using a small ruling pen, a small brush, or
a "Speedball" pen. Cover all parts of the layout, for only those parts of the copper
foil covered by the ink will remain after etching. Allow the ink to dry.
Ordinary plastic-base Scotch electrical tape makes an excellent tape resist.
It is furnished in some kits. Narrow strips may be cut from the standard width using
an "Xacto" knife, a razor blade, scalpel, or similar tool. Small circles, for terminal
connections, can be punched out with a small hand paper punch. The tape is simply
applied to the copper foil to cover the traced layout pattern, then burnished down
with a smooth, hard tool. A good burnishing tool can be made quite easily by rounding
the end of a wooden dowel peg.
Double-check the circuit board after applying the resist. Compare it to the original
layout. If you find you've made an error, correct it. Ink resist may be removed
by using a hard (ink) eraser. Tape resist is simply peeled off. Reapply the resist
to correct the error.

Fig. 2 - A "typical" board which illustrates the important
points that you should remember in making up your own printed-circuit layout. It
does not represent specific circuit.
Posted April 18, 2022 (updated from original post on 10/19/2016)
|