February 1944 Popular Science
[Table of Contents]
Wax nostalgic about and learn from the history of early
electronics. See articles from
Popular
Science, published 1872-2021. All copyrights hereby acknowledged.
|
Fundamentally, not much has changed in the
way binoculars are constructed versus in 1944 when this article appeared in
Popular Science magazine. Manufacturing methods have, of course, been updated.
At the time nearly all binoculars used a "porro prism" (PP) design (named after
inventor Ignazio Porro),
but today many employ a "roof prism" (RP) configuration (named after... a roof).
A search of the pros and cons of each turned up mostly a regurgitation of the same
information, much of which I consider to be very biased toward roof prism types,
including claims that RPs are waterproof and PPs are not (my
Nikon Action EX 7x50 PP binocs are water proof), and that RPs use antireflective
coatings whereas PPs do not (my Nikon PPs have antireflective coatings). As is typical
with most products, the features largely depend on what you pay for the binoculars.
High-end telescope maker Celestron has a good write-up on
porro prism vs. roof prism binoculars. Astronomers, incidentally, prefer prefer
prism binoculars over roofing prism types.
How Binoculars Are Made
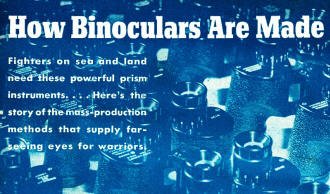
Photographs taken by Robert F. Smith at Universal Camera Corp., New York, N.
Y.
Fighters on sea and land need these powerful prism instruments... Here's the
story of the mass-production methods that supply far-seeing eyes for warriors.
America's front-line fighters must see more than meets the eye. In every battle
zone - land, sea, and air - they're called upon to perform ocular miracles. It's
their job to unmask camouflage, dissect heat and haze, and scan hopeless distances
to get information that spells victory. They must spot the enemy before he sees
them. And they're doing it with American-made prism binoculars, now in mass production
for the first time.
The ingenuity that made this possible has been rewarded with an "E" presented
by the Army and Navy to the Universal Camera Corporation of New York. On the verge
of ruin in 1940, when war blacked out its European film markets, this firm rallied
to take a top place among war industries. Before the end of 1943, its production
hit 11,000 binoculars a month for our armed services. That means turning out 150,000
optics (lenses and prisms), to say nothing of fabricating and assembling more than
a million metal parts.
Grinding the Lenses
Grinding the objective lenses of prism binoculars is done mechanically with wax-surfaced
wheels while a solution of red oxide of iron flows over the work (above right).
Batteries of these machines, whose grinding wheels are automatically controlled
as to speed and pressure, now mass-produce lenses formerly turned out laboriously
by skilled craftsmen. So precise are the machines that they can smooth down a lens
to a tolerance of 1/100,000 of an inch. During milling and polishing, lenses get
116 inspections
Making the Prisms
Here a group of prism blanks, made of light barium crown glass, are being placed
in a diamond cutting machine. Precisely machined metal blocks are used as holders
for the prisms, which are set into recesses and helf fast with wax and binding strips
After being rough-cut, the prism blanks are set in the niches of a milling machine
that revolves in a bath of grinding fluid. As the machine turns, it brings one side
of each prism into contact with a polishing disk, which is beneath fluid's surface
With the faces and sides of the prism now carefully polished, the next step is
to bevel all its edges. This is a hand operation in which the prism is held against
a grinding wheel, while a stream of ordinary water is played over the stone as a
grinding fluid
A clamp that will hold it firmly in the binocular is about to be placed on a
prism. At this point, the prisms have been paired off so that one having a plus
deviation in the verticality of transmitted light is coupled with one of equal minus
deviation
Assembly
The housing for a binocular is cast from scrap aluminum, machined, then covered
with strips of Vinylite, which has the texture of leather. A soldering iron fuses
strips into one piece
Universal has tossed out all the old, traditional methods of making binoculars.
Otherwise, it still might be slogging along neck-deep in red ink. It has turned
a highly specialized art into a task for machines tended by unskilled labor. It
has speeded the whole cycle of production to a degree undreamed of heretofore.
In preparing flawless faces of lenses or prisms, the basic steps are roughing,
grinding, and polishing. The custom is to rough out each glass blank separately,
then mount them in a mold. After that, for the grinding and polishing operations,
the mold is spun against abrasives. When one side is ground, it is turned over and
ground on the other side. This procedure goes on through all stages of grinding
and polishing. It's tedious and time-consuming.
A set of prisms is here being placed in one barrel of the binocular. Note that
the other barrel is covered to prevent accumulation of dust, which must be guarded
against at every stage of assembly
To reduce loss of light caused by surface reflection, optical elements in binoculars
are being coated experimentally with magnesium-fluoride vapor. Tests indicate coated
pieces transmit about 99 percent of light
At Universal's plant, sparks fly by application of a three-in-one process. Blanks
are mounted on a mold that carries them through roughing, grinding, and polishing
as one continuous operation for each side, What's more, molds are so designed that
unskilled hands can easily insert blanks. This simplifies the formerly complicated
task of mounting. For the final polishing - a job that once required fine judgment
and skilled hands - Universal automatically applies a liquefied oxide that not only
does just as well, but also minimizes chances of human error. In all, this new method
of making binoculars has established a manufacturing precedent that will endure
long after the war is over.
Objective lenses, consisting of two lenses cemented together and fitted into
metal rings, are immediately screwed into place after a suction tube (bottom) removes
dust
Assembly of the binocular is completed with the mounting of the eyepiece. This
part comprises the field, or collective, lens, a short barrel, and two lenses cemented
together to form the eye lens
For the present, however, its task is to speed the flow of urgently needed binoculars
to our fighters on land and sea. With the aid of these precision-built instruments,
Americans in all services will be able to see better and fight better.
Inspection
An illuminated screen containing square's on which fine lines are drawn is used
to test the ability of the binocular shown above, to distinguish two parallel lines
when they subtend five seconds of arc at the instrument. At the left, a military
binocular is checked to see if its two ocular axes are parallel. The girl above
is using an auxiliary scope, an ordinary telescope placed over one of the eyepieces
of a binocular to magnify its normal resolution. A binocular is also sighted on
actual object to test clearness, color dispersion, and astigmatism. And, finally,
it is placed in a tank of water to see how waterproof it is, and then dropped six
feet into a sand pit to test its ability to withstand rough handling
Posted November 6, 2023
|