December 1931 QST
Table
of Contents
Wax nostalgic about and learn from the history of early electronics. See articles
from
QST, published December 1915 - present (visit ARRL
for info). All copyrights hereby acknowledged.
|
There are still a lot of people who wind
their own coils, whether it be for an amateur radio rig or for work in the lab.
I know I've wound many a coil around a drill bit or wooden dowel. This simple coil
winding machine that appeared in a 1931 edition of QST magazine would be a handy
addition to anyone's bag of tricks, especially if find yourself winding single-layer
coils that have a fixed space between the windings. The home stores like Lowes and
Home Depot sell small pieces of oak that would be perfect for this kind of project.
A little stain and a coat of varnish would give it a real vintage look. Use your
soldering iron to burn your name onto the base.
A Winding Machine for Spaced-Turn Chokes
By W. H. Heathcote, ZT6X
Space-wound chokes are made easily if one has a screw-cutting lathe, but these
expensive items seldom form part of a ham's equipment. The following description
of a machine for winding spaced chokes will, I trust, be of assistance to hams not
in possession of lathes. Most of the material will be found in the junk box of the
average ham, but even if all the material has to be purchased the cost would be
negligible. Since spacing the windings decreases the distributed capacity of a choke
and - more important - raises the breakdown voltage at the end turns where the voltage
per turn is always highest in a transmitter of any power, the time spent in making
the machine is well worth while.
Referring to Fig. 1, it will be observed that a traverse motion of the choke
form along the horizontal rod is obtained when the handle is turned in a clockwise
direction. The nut soldered to the circular plate through which the threaded spacing
rod screws moves the choke form along, the number of turns per inch being dependent
upon the number of threads per inch on the spacing rod.

Fig. 1
A piece of wood approximately 16" x 4" x I" will serve nicely as a baseboard,
and to this two blocks of wood to carry the bearings are screwed; these are 2 3/4"
(in height) by 3" x 1/2". One is fixed about a half inch from the edge of the board
and the other 8 inches away from the first one. Another block of wood 2 1/22 inches
in height, also 3" x 1/2", is mounted 4 inches distant from the second block, and
to this last block the circular plate is fixed. The main shaft is a piece of rod
12" in length threaded a half inch at one end and 1 1/2" at the other. The purpose
of the sleeve (see Fig. 1) is to enable the choke form to be inserted and
removed with a minimum of trouble. If the main shaft is released from the socket
on which the spacing rod is soldered, it is only necessary to unscrew the wing nuts
on the collar and the main shaft can be instantly withdrawn, thus releasing the
choke form. The sleeve is 4" in length and of sufficient diameter to allow the main
shaft to pass through freely. A collar about 3/8" in length is soldered over the
end of the sleeve nearest the conical disc. Without this collar the tubing is likely
to cut into the conical disc if it is made of hard rubber or other soft material,
especially if a thin tube is used for the sleeve.

Fig. 2
The bearings are both 1/2" in length. No.1 can be a piece similar to that used
for the sleeve. No.2 will have to be large enough in diameter for the sleeve to
pass through. The bearings are soldered to brass "saddles" and screwed to their
respective bearing blocks.
The spacing rods are four inches in length. An assortment of rods with different
thread pitches will allow a choice of different spacings between turns. One end
of each rod is soldered to a socket (which may be made from an old binding post)
as shown in Fig. 2. Care should be taken to see that sufficient space is left,
after soldering the rods to the sockets, for the main bearing shaft to screw firmly
in the socket. A simple way to insure this is to screw a piece of wood halfway through
the socket, place it upright in a vise and after centering the spacing rod in the
socket run the solder into the surrounding cavity.
The circular plate is a disc of 10 gauge brass 3" in diameter. Holes slightly
larger in diameter than the spacing rods are bored a half inch from the center.
Through the center bore a hole to enable the plate to be held in position by means
of the small bolt and wing nut on the block of wood on the baseboard. Solder nuts
corresponding to the gauges of the spacing rods over the holes already bored for
that purpose.
The handle is very simple and needs little description. A nut is soldered on
the side nearest the sleeve. The one shown on the outer side acts as a locknut.
The collar is about 1/4" in thickness with holes bored and tapped at opposite sides
for the wingnuts. The guide (Fig. 2) can be made either of wood or hard rubber.
Notches are made with a file every 1/8" or 1/4" along the top for holding the wire
steady when the winder is in operation. The conical discs can be made of tin, hard
rubber or wood.
The machine as described above will only make a winding 3" in length. Two chokes
could be wound and placed in series if it were necessary to wind a choke on a form
greater than two inches in diameter. Hard rubber or fibre tubing cut into 4-inch
lengths is used by the writer as choke forms. After the shaft, discs and choke form
have been placed in position the wing nuts on the collar are tightened up and on
turning the handle pressure on the sleeve will center and tighten up the form, after
which the locknut at the handle end of the rod can be fitted.
When winding chokes of say 100 turns, to decrease the distributed capacity it
is a good idea to use a spacing rod with about 50 turns to the inch and after winding
25 turns remove the wire to the next notch cut on the top of the guide. The same
procedure is followed after each 25 turns wound, the result being a spaced choke
with additional spaces between sections.
A number of improvements will suggest themselves to hams; in fact I have made
several myself, but to make things as clear as possible I have shown and described
the machine originally built.
Better Filtering
Many amateurs do not realize that there is often a real advantage in the use
of tuned filter circuits for power supplies, since the amount of inductance and
capacity necessary for a given degree of filtering is much less than that required
in the more common filter arrangements. Here is some interesting information from
Franklin Offner, W8AJZ-W9FTO:
"A few days ago I was working with W3AH, measuring the ripple voltage from various
condenser-choke combinations. The ripple voltage was measured with a one-ma. rectifier-type
voltmeter in series with a 2-μfd. condenser. Our results, though only an indication
of what can be done, lead me to believe that hams can do a lot better than merely
pile on the microfarads and henrys in single or multiple section filters.
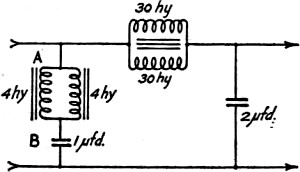
Fig. 3
"We tried various combinations of the following: a 1-μfd. condenser, a 2-μfd.
condenser, an RCA double 30-henry 80-mil choke and a couple of Stromberg-Carlson
250-mil 4-henry chokes (43¢ each) all used simply because they were available. With
the best combination of chokes in the brute-force arrangement using 1 μfd. on
the input and 2 on the output, the ripple was around 6 volts, from a 550-volt (each
side) transformer, full wave, at 100-mil load. Then the circuit of Fig. 3 was
hit upon, and the ripple voltage output from this combination was only 0.8 volts.
Evidently the two 4-henry chokes and the 1-μfd. condenser were series resonant,
since either adding to or subtracting from capacity or inductance caused a large
increase in ripple output. It is probable that by varying the values of the condenser
and choke in the series resonant portion better filtering would be obtained and
also by more careful adjustment of the inductance of the choke, "A," possibly by
using one with variable air gap, in order to make the combination resonate at exactly
120 cycles. Obviously the choke used at "A" may be of low current-carrying capacity,
since it carries no d.c. This point is the big advantage of this circuit over one
using tuned traps in series with the output - that is, the chokes carry no d.c.
and therefore their inductance does not vary with the load drawn.

Fig. 4
"We intend to do more work on this circuit, and would appreciate hearing from
anyone else trying it."
Feeder Switching
In the October Experimenters' Section two diagrams were shown for switching feeder
condensers from series to parallel, in one of which, Fig. 7, a connection was
unfortunately omitted. The right-hand feeder should be connected to the right-hand
switch blade; if this is not done the diagram will not work when the switch is thrown
to the" parallel" position.
Several letters were received from readers who caught this mistake, with Clem
Wolford, W8ENH, and Robert A. McConnell, W8FJ, both suggesting a switching arrangement
which is quite the simplest we have seen. Fig. 4 is the diagram. The switch
is a double-pole single-throw affair, the condensers being in series when it is
open and in parallel when closed.
Posted March 12, 2020 (updated from original post on 10/24/2012)
|