October 1937 Radio-Craft
[Table of Contents]
Wax nostalgic about and learn from the history of early electronics.
See articles from Radio-Craft,
published 1929 - 1953. All copyrights are hereby acknowledged.
|
There is no arguing that digital
multimeters are vastly superior to analog meters in many - maybe even most - ways.
However, analog meters still have applications that make them indispensible in situations
like monitoring slow variations in parameters and for quick visual approximations
of values. One example is looking for variation of voltage or current levels under
varying loads. Yes, digital instruments are available that emulate an analog display
in certain modes, but that just proves the point of he usefulness of an analog movement.
Another is the familiar control panel filled with meters where clusters are trimmed
to be centered or at one extreme when the system is running optimally. Yes, effectively
the same result can be obtained with digital readouts and colored status lights
- and often is - but for a glancing status scan, it's hard to be the needle (IMHO,
of course). Here is my vintage
Heathkit IM-17 Utility Solid-State Voltmeter. This is
Part 2 of this series.
How Dependable Are Your Meter Readings?
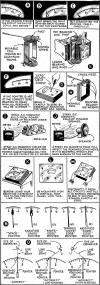
Fig. 2 - Illustrations detailing the points discussed in
the text.
Rare indeed is the Service Man who realizes just how, why, and to what extent
his service meter readings may be inaccurate - and how much it really matters! This
article explains, simply and expertly, the entire subject of meter accuracy. The
author's published works include his well-known "Radio Physics Course," "Modern
Radio Servicing," etc.
By Alfred A. Ghirardi
Part I
How accurate is the voltage reading you just took on that receiver? How accurate
are the meters you are using in your service work, anyway?

Fig. 1 - Breakdown chart of the various causes of errors
in test meters.
Are you one of those trusting Service Men who think that just because a meter
is fairly new or expensive, it will give readings that are 100 per cent accurate
at any point on the scale? Or, on the other hand, are you one of the suspicious
but disillusioned type who has tried to check the accuracy of the meters in his
test instruments, only to find that no two readings agree exactly? In either case,
you (in common with most radio Service Men) are the victim of an incomplete, or
inaccurate knowledge of electrical instrument construction and operating characteristics,
for, anyone closely associated with electrical instrument design and manufacture
is well aware that errors exist in all instruments, and will admit it freely. Fortunately,
the entire subject of meter accuracy is fairly simple - and interesting. Perhaps
we can clear up, in this series of articles, some of the more troublesome difficulties.
No Meter is 100 Per Cent Accurate
First of all, get this fundamental fact firmly in your mind: no commercial type
electrical indicating instruments are guaranteed to read 100 per cent correctly
at every point on the scale - only very expensive laboratory-type instruments approach
such perfection.
That means that you cannot, and should not, expect the readings you take on your
servicing meters to be 100 per cent accurate. They really don't have to be - but
that's another part of our story. What you should know is, how large the errors
are, what their origin is, how you can minimize them, and whether they will seriously
affect the usefulness of your measurements.
The accuracy, sensitivity, and reliability of an electrical instrument are determined
by its design, the quality of the materials used in it, the care taken in its construction,
the accuracy with which it has been assembled and calibrated at the factory, and
how roughly it has been handled since made. In order to make meters that can be
priced within the reach of the average user, accuracy has to be sacrificed somewhat.
Meters can be purchased for from less than a dollar up to several hundred dollars.
Naturally, the more one pays for an instrument, the better the quality of materials
used in it and the more accuracy and care exercised in its workmanship and calibration.
The general run of meters used in present-day high-grade servicing instruments represent
a good common-sense compromise between accuracy and price - they provide sufficient
accuracy (around 98 per cent for D.C. instruments and 95 per cent for rectifier
type A.C. instruments) for the general run of servicing measurements to be made,
and are priced within the limits of the Service Man's pocketbook. Their manufacturers
deserve unstinted praise, for by working out clever designs, careful selection of
materials, and taking advantage of every technical advance and possible manufacturing
economy, they have succeeded in making really fine, rugged, instruments available
to the Service Man at reasonable cost.
But the Service Man should realize that these instruments are not perfect - no
"manufacturer claims them to be! Practical construction difficulties make absolutely
precise .instruments unobtainable. A knowledge of the errors likely to occur, the
origin of these errors, and the means used to make them negligible (or as small
as possible) is of value in enabling one to use electrical instruments intelligently
and obtain the best results from them under working conditions.
What Causes the Errors?
Now that we are reconciled to the fact that errors do exist in measurements made
with electrical instruments, let us see what they are and what may cause them.
All of the common inaccuracies have been grouped and arranged for quick reference
in a convenient chart in Fig. 1.
Notice that there are 4 main sources of inaccuracy: (1) those which are inherent
in the instrument itself due to its design and construction, and which may be present
even in brand new instruments; (2) those which have developed, in the instrument
as a result of its constant usage, rough handling, etc.; (3) those which occur because
of the particular way the instrument is used, or the conditions under which the
measurement is made; and, (4) those which occur through inaccurate reading of the
pointer position by the observer. In the chart, each of these is further broken
down into its contributing causes.
Let us review these contributing causes of error briefly; so that we may understand
why they may be present and what effects they have on the readings.
(A) Temperature errors due to self-heating. Most instruments
contain sources of heat, such as moving coils of fine wire, springs, shunts, multiplier
resistors, rectifiers, etc., through which the currents flow. This heat tends to
cause a rise in the temperature of the various parts of the instrument - resulting
in a change in the resistance of these parts, a consequent change in the current
flowing, and a change in the deflection of the pointer. ("Carbon" resistors have
a negative coefficient and hence decrease in resistance value.)
Naturally, the error which may result depends
upon the value of the current or voltage under measurement and upon the length of
time that the instrument is kept in the circuit. Fortunately, since the currents
involved in the measurements made in radio service work are fairly small and the
instruments are kept in the circuit only for a very short time, this source of error
is not a very great problem.
By making the shunts and multiplier resistors of resistance materials which have
a very low temperature coefficient of resistance, their resistance change due to
heating is minimized. The increase in resistance of the copper movable coil is compensated-for
by using a control-spring material which produces a restraining spring that weakens
just the right amount with change of temperature so as to offset the effect of the
resistance increase of the movable coil. By employing these refinements in design,
the actual error due to self-heating in commercial instruments is kept so low that
it is negligible.
 (B) and (C) Frequency and waveform errors.
Errors due to variation of frequency (A.C. measurements), seldom bother
the Service Man, because these errors are negligible for the frequencies of the
A.C. circuits he has occasion to make measurements on. The same is true of waveform
variation, which is, to a certain extent, analogous to variation of frequency.
(D) Mechanical errors. The quality of the control springs used
in an electrical instrument has a very important bearing on its permanency and accuracy.
The springs are such important items in the meter, that the rigid inspection they
undergo before the meter leaves the factory of any reliable manufacturer makes them
almost certain to be in perfect condition. What may happen to them later will be
discussed.
Another ·mechanical error may be caused by friction
in the jeweled bearings. This trouble also, has been reduced to insignificant proportions
by proper inspection at the factories. However, as we shall see presently, rough
handling, or excessive wear may cause this trouble later.
(E) Calibration errors. The scales for very inexpensive instruments
are engraved or printed all in one batch, on the assumption of a particular deflection
law for a given type instrument; generally the individual instruments are then adjusted
by trial to make their deflections fit the scales as closely as possible. Naturally,
such meters do not give accurate readings; but since the sale price is so low, the
cost of individually calibrating each instrument would be prohibitive, and there
is no other alternative.
For the better grade instruments, it is common
practice to calibrate the scale of each instrument individually. It is not necessary,
of course, to determine every scale division by test, especially on direct-current
instruments with nearly uniform scales. It is usually considered sufficient to check
at only a few points on the scale of a D.C: instrument by actual test. The intermediate
points are filled-in, sometimes by hand, preferably by a mechanical method. Of course,
if the shunts, multiplier resistors, or condensers used in the instrument are not
accurate in value, this will affect the accuracy of the entire instrument. Any subsequent
changes in these values due to "aging" of the resistors, condensers, control-springs
or magnets, will also affect the accuracy. (Scales, even, are preferably of metal,
for permanence.)
(2) Inaccuracies Developed Through Use .and Handling of the Instrument
A good electrical instrument is as fine and delicate a piece of mechanism as
a fine jeweled watch. It should be handled with just as much care as such a watch,
if its original accuracy is to be maintained; for many things may happen to it at
any time, impairing its accuracy and reliability. Such a simple thing as a bump,
or a fall, always possible with portable instruments, may have serious consequences.
With permanently-installed instruments, a knock or a blow, continual vibration,
effect of powerful nearby magnetic fields, overloads or other disturbances - any
of these may affect instruments to such an extent as to make their readings unreliable.
(F) Bent pointer and overload. If too
great a voltage is applied across the meter terminals (or stated in another way,
too much current is allowed to flow through the meter coil), the pointer may strike
against the end stop with sufficient violence to bend it. See Fig. 2A. If this
occurs, never bring the pointer back to zero by means of the zero-adjusting screw,
for this will not bring the indications into even approximate agreement with the
scale markings. It will bring the moving coil into an initial position far different
from that which it occupied when the initial calibration was made. See Fig, 2B.
The correct thing to do is to straighten the pointer itself, in order to bring it
back to zero. (Fig. 2C.) Errors due to bent pointers are quickly detected (in
most instruments) by a lack of parallelism between the pointer shaft and the scale
markings.
How much overload a given meter will stand depends upon its design, and how the
overload is applied. Overloads of reasonable magnitudes will not harm properly-designed
instruments. If the overload is applied for only a short time, and gradually, so
there is no violent movement of the pointer, the instrument will most likely stand
considerable overload without damage. (The meters of at least one prominent test
instrument manufacturer are designed to stand overloads as high as 10 times the
normal value.) However, if the overload is applied suddenly, so the movement is
violent, a much smaller amount of overload will surely bend the pointer and also
possibly dull the pivots or pit the jeweled bearings with resultant lagging and
sticky action.
Incidentally, an overload of the wrong polarity, forcing the meter needle backward
off-scale is very hard on meters and should be cautioned against. It is always good
policy to start measuring an unknown quantity with the range selector of the instrument
in the highest range position, gradually backing it down until a range is reached
where the needle deflects without going off-scale to the right. This, of course,
is the range where the user will receive his most accurate results, and this policy
of working down to the proper range will save many a meter from a burn-out due either
to too much deflection forward or, a disastrously high voltage or current of the
wrong polarity (as far as the meter connections are concerned).
(G) "Zero" shift. If accurate readings
are desired, it is apparent that the pointer must stand exactly at the "zero" point
on the scale when no current or voltage is applied to the instrument.
If the pointer is not at the zero position to start with, it is evident that
all indications at other points on the scale will be in error. Practically all commercial-type
meters are provided with a zero-adjustment screw (see Fig. 2G), which varies
the tension of one of the control springs, allowing the meter pointer's "at rest"
position to be adjusted over several scale divisions, so that it may be centered
exactly over the position marked "zero" on the meter scale.
Always make sure that the pointers on your instruments are in the correct "zero"
position before taking readings! If the zero error is found to be beyond the range
of the adjusting screw, or if a sudden zero error of considerable magnitude is observed,
it is safe to assume that the instrument needs checking and possible repair.
When "zero"-adjusting a meter be careful to a void "parallax error" (explained
later). This is particularly important when "zero"-adjusting most ohmmeters, for
in these instruments the "zero"-adjustment screw does not adjust the meter pointer
position directly but usually adjusts a resistor which compensates for variations
in the potential of the battery supplied with the instrument. A fresh battery will,
of course, apply a higher voltage to the instrument circuits than after it is partially
discharged. Furthermore, because the resistors used in these meter circuits are
not absolutely precise in value, there is some variation between the accuracy of
the various ranges of the instrument. Therefore, each range of the instrument should
be "zero"-adjusted separately - just before using.
The Megohm ranges of ohmmeters are usually powered by a miniature power supply
working from the house or shop line voltage. Variations in this line voltage can
be, and should be compensated-for by means of the Ohms Zero Adjuster, or whatever
the manufacturer calls the "zero"-adjusting control.
Do not confuse simple "zero error" with that due to a bent pointer. If the pointer
is very much off-zero because it is bent, it should not be brought back to zero
by manipulating the zero-adjusting screw; for such an adjustment brings the moving
coil into an initial position far different from that which it occupied when the
initial calibration was made. The bent pointer itself should be straightened!
(H) Spring errors. The springs play
one of the most important parts in maintaining the accuracy of the instrument; for
they not only conduct the current to the movable coil, but also supply the "restoring"
torque (or twist) which resists the "actuating" torque of the movable coil, and
then returns the coil and pointer to the "zero" position when the current is shut
off. Any change in the "restoring" torque produced by the springs will cause a change
in the position of the movable coil and pointer - causing an error in the readings.
Within the past few years, phenomenal metallurgical advances have been made in
spring design which almost eliminate the "fatigue" and "aging" of springs which
manifested themselves in a "drift" of calibration in older instruments. The improved
springs used in instruments of reliable manufacture render negligible any probable
error from this source, so long as they are not subjected to mechanical or electrical
abuse.
Of course, if the springs have become overheated by prolonged abnormal current
flow, they will lose some of their "temper". This will decrease their "restoring
torque", and make the instrument mere sensitive. (See Fig. 2, D and E.) Consequently,
its readings become inaccurate insofar as its original scale calibration is concerned
- and such errors may often be of considerable magnitude. This abuse of the springs
by prolonged overload is difficult to detect because, as a rule, the meter seems
to operate in a perfectly normal manner, no sluggishness or stickiness being evident.
The springs may also become "kinked". This fault will frequently manifest itself
by the fact that the reading at a certain point of the scale will be different on
"increasing" from "decreasing" values. Another error may creep in from "softened"
springs which sag. These cause uneven torque, and an abnormal "zero error" of the
pointer.
In general, the control springs of an instrument should be maintained in as nearly
perfect a mechanical condition as possible by not abusing the instrument by serious
overload, rough handling, etc. If the springs of an instrument have received any
form of damage, it should be returned. to the manufacturer, or an authorized repair
shop, for repair, if accurate measurements are to be made with it.
(I) Bearing friction. The hardened
and highly-polished steel pivots· and the almost-frictionless sapphire jewel bearings
which support the movable coil are subject to wear and damage. (See Fig. 2E.) They
are finely shaped and polished, and accurately adjusted before the in-strument leaves
the factory; but friction may develop, due to excessively worn or damaged jewels
or pivots. Rough handling of the instru-ment, overloading, dropping and tampering
are all common causes of damage to the bearings.
Friction in the bearings usually manifests itself in a stickiness and lag of
pointer movement, and a noticeable uncertainty in its zero position. Bearing friction
will not usually cause errors in the readings, provided the instrument is gently
tapped when the readings are being taken; but since its causes are likely to be
productive of more serious results, they should be eliminated whenever possible.
Friction may also be caused by rubbing of the pointer On the scale, or on fine
fibers loosening from the substance of a paper scale and projecting out so the pointer
touches them. This trouble may become evident only during certain atmospheric conditions,
and usually at certain parts of the scale; and it may be difficult to discover.
Small particles of foreign matter which have worked their way into the short
air gaps of the magnet generally cause "sticky" operation and make the pointer indications
erratic.
It is interesting to note that "sticky" meters due to foreign substances lodging
themselves in the movement seem to rank highest among the most frequent meter repairs
not due to owner negligence or carelessness. Sticky action is apt to occur even
in new instruments, due to the jarring and shaking received during shipment. Although
manufacturers take extreme care to insure receipt of the instrument in perfect condition
and despite the care taken in assembling the meters, "trash" in the form of minute
metal filings and bits of insulation or fibre may work into the movement. A meter
service station should remedy this because the average radio Service Man is not
capable of handling the delicate job of cleaning out and adjusting the movement.
Anyway, the usual manufacturer's guarantee will generally cover the cost of the
adjustment, if it becomes necessary, within about 90 days of the purchase date.
A "sticky" meter may be detected immediately. Sticky or defective meters should
be repaired at once rather than "borne with" as a man who uses an instrument which
is not in 100% working order will subconsciously build up a psychological "mad"
at the instrument's manufacturer. If it is repaired, he soon forgets that there
was anything wrong with it.
"Backlash" in the moving parts is due primarily to loose fits in the. This trouble
is not common, nor serious, since errors due to it may be materially reduced by
gently tapping the instrument while taking the readings.
J) Electrical troubles. Under this
classification are those troubles which may develop in the electrical circuits of
the instrument after it has been assembled, tested and calibrated. Poorly-soldered
joints, loose or broken conductors, and partial or complete "short-circuits" or
"grounds" are some of them. It is surprising how many loose or badly-soldered joints
develop in supposedly well-made instruments, unless the manufacturers are careful
to inspect them rigidly at the factory.
"Opens" due to breakage of the fine wire comprising the movable coil or that
employed for the multiplier resistors in voltmeters, have given trouble in some
models of instruments. Of course, in such cases, the meter fails to operate either
on one or more ranges - or altogether, so the trouble quickly makes itself evident.
These electrical troubles can usually be detected by observation of the instrument
for erratic action. When they are detected, they usually require a careful and complete
repair before the instrument can again be considered reliable for service.
The copper-oxide rectifiers used in rectifier type A.C. instruments can cause
an increase in meter inaccuracy. These copper-oxide rectifiers are inherently delicate
and can be easily overloaded. The average rectifier of this type will pass a maximum
of but a few milliamperes, above which the rectifier "breaks down." This condition
appears to be present in any A.C. measuring-meter circuit whether it be strictly
a series-dropping resistor type or one in which condensers and resistors are used.
Care should therefore be exercised in the application of A.C. voltages to these
meters, for overload often results in a damaged rectifier and lowered A.C. voltage
readings. The rectifiers cannot be repaired and are never guaranteed by the original
manufacturer. Therefore, damaged rectifiers should be replaced by the instrument
manufacturer, or by some reliable meter repair firm, for they sometimes go bad even
while being placed in the instrument. The copper-oxide rectifiers should never be
touched with the hands as chemicals in one's perspiration will usually cause early
rectifier failure.
The ratio of the rectified current to the applied current may change for a given
rectifier. Troubles such as the above cause this ratio to drop to sometimes half
the original ratio. Variations are also possible due to variations of temperature,
humidity and the amount of current applied to the rectifier each time it is used
for a measurement. In other words, the rectifier will have one ratio when say 0.1-ma.
is applied, another when 0.5-ma. is applied, etc.
(K) Magnet weakened. Properly designed
permanent magnets of the types which are being used in recent high-grade instruments
will stand a surprisingly large amount of rough handling before their magnetic strength
will change sufficiently to result in incorrect readings. Other parts, such as the
jewels and pivots, springs, etc., which are more susceptible to damage by mechanical
shock, are more troublesome in this respect. However, the safe rule is to handle
your instruments carefully and avoid all mechanical jolts and shocks.
(3) Inaccuracies Due to Way Instrument Is Used, Or Conditions Under Which Measurements
Are Made
There are several inaccuracies which are apt to creep into measurements made
with electrical instruments simply because of the way the instrument is used, or
the conditions under which the measurements are made. Errors which may be present
when a particular instrument is used for one measurement may not occur when it is
used again under different operating conditions - and vice versa! Some things to
watch for will be pointed out in Part II.
Figure 2 includes illustrations of important elements in meter construction,
which the Service Man may be interested to note, as, to a limited extent they are
self-explanatory. However, the detailed analysis of these elements (Figs. H to O,
inclusive) constitutes important, basic knowledge which every technician should
possess. This information, and considerably more, will appear in Part II of this
useful article.
Read Part II of this article; it will discuss Inherent Meter Accuracy (or inaccuracy).
The author of this vital article is also author of "Radio Physics Course, "Modern
Radio Servicing," and "Radio Field Service Data" - al of them valuable contributions
to the field of literature for the practicing radio Service Man.
Posted September 10, 2020 (updated from original post on original 9/28/2016)
|