June 1940 Radio-Craft
[Table
of Contents]
Wax nostalgic about and learn from the history of early electronics.
See articles from Radio-Craft,
published 1929 - 1953. All copyrights are hereby acknowledged.
|
Do you know what a "gimmick" is in the RF
circuit world? If you have ever had the occasion to repair or recondition inductors
(coils, chokes, etc.), then you have probably seen one and probably didn't know
what it was. Read on to learn about a gimmick capacitor (they yield about 1 pF/inch,
see Stackpole ad to the left and
twisted pair impedance
calculator). Working with the tiny wires on those old coils can be a real challenge.
Words you hadn't uttered in a long time tend to move to the forefront of your memory
in the process. Having struggled with a few multi-layered RF coils from old radios,
I am familiar with the intricacies of trying to use fat fingers to wind and splice
40-gauge enameled wire in spaces 1/8-inch wide. Many of those older coils are wound
in thin, tall rings whose wires have a tendency to slide off the sides during manipulation.
A useful trick not covered in this article is to make thin wood (I use balsa, but
pine or thick cardboard will work) forms to press against the sides and keep everything
in place. There are lots of great tips here.
Servicing R.F. Coils
This article, No.1 of a series, shows Servicemen how to repair radio-frequency
coils so as to save the time and money otherwise involved in making exact replacements
or in waiting for factory repairs. Much valuable and practical information you cannot
find in books is published here for the first time.
Lawrence V. Sorensen

Fig. 2 - Typical replacement of primary windings.
|
The question of replacements for defective radio-frequency coils has long been
a nightmare to Servicemen. Many of these technicians, realizing the amount of design-work
embodied in such coils, have insisted upon exact duplicate replacements or that
the defective coil be repaired by a coil company. In either case, considerable delay
often resulted.
Most Servicemen apparently have not realized that the part of the coil that fails
in normal service is the part which was manufactured to rather broad tolerances
of inductance, and that this part (the primary) can easily be replaced since it
has only a minor influence on the "tracking" of the receiver circuits. There-fore,
if the defective primary is replaced, the original coil with its accurately-controlled
secondary inductances can be salvaged.
The Serviceman can give best service to his customers, when R.F. coils fail,
if he is familiar with replacement primary windings and knows how to use them, and
repairs the coil himself.
Repairs - In Detail
The advantages of being able to repair radio frequency coils are obvious to every
Serviceman. It remains only for him to convince himself that he, personally, can
do the job.
Many Servicemen, who are well able to correct trouble in any make or type of
receiver, hesitate to tackle the repair of an R.F. coil because of inadequate knowledge
about the design constants of such coils, or because they believe that only trained
feminine hands can properly handle the fine wire used. The first objection has been
overcome by studies made by the Meissner Mfg. Co. which has determined that for
any Broadcast-band Antenna or R.F. coil, one of 3 values of inductance will serve
admirably, and as far as replacements for Shortwave primaries are concerned, these
primaries usually consist of only a few turns of wire which can be replaced with
an equal number of turns of No. 36 S.S.E.
The question of ability to handle the fine wire of which broadcast primaries
are made can easily be settled after a few minutes' practice with a piece of sandpaper
and a piece of No. 36 S.S.E. or No. 38 S.S.E. wire, or the outside lead of one of
the replacement primary windings. (If the outside lead should break off too short,
a few turns can always be peeled off the coil to give the required lead length without
materially altering the performance of the coil. This, of course, positively is
not true in the case of secondaries, which must be held to close tolerance of inductance.)

Fig. 1 - Sandpaper for cleaning wire.
It has been found that if a piece of No. 00 sandpaper is folded and cut in accordance
with the sketch in Fig. 1 and is held between the thumb and forefinger the
insulation - first the fabric, then the enamel - can easily be stripped off of the
wire no matter how fine the wire, if appropriate pressure is used on the sandpaper
while sanding the wire. Much too little pressure will require a long time to strip
the insulation, while too great a pressure will break the wire. A few moments' experiment
will quickly inform the Serviceman of the proper pressure to use. There is one point
that should be stressed, and that is, that in his determination not to break the
lead, the Serviceman should not make the mistake of failing to properly clean off
the enamel. If the latter insulation is merely scratched through in a few places,
it is not possible to make a good connection. The solder will not stick to the few
bright scratches so made. The wire must be thoroughly cleaned.
A few trials at cleaning size 38 enameled wire will soon convince the Serviceman
that he can do just as good a job of cleaning the wire without breaking it as can
the trained fingers of feminine coil operators, although undoubtedly he will be
somewhat slower. A trick that may help to avoid breaking the wire, is to rub the
2 surfaces of the sandpaper together before attempting to remove any insulation.
This action removes the high spots on the sand-paper which tend to grab the conductor,
and makes the action of the sandpaper smoother and much easier to control.
Replacements - Step-by-Step
The following section is a step-by-step set of directions for replacing a defective
primary on a radio-frequency coil. A typical group of replacement Primary Windings
is shown in Fig. 2. Some sections of the directions may seem obvious when read,
but may easily be overlooked until too late if the task of replacing a defective
primary is started without careful consideration of each step, in sequence, because
once a coil has been torn apart it may be too late to observe certain details, that
it may be necessary to know, in order to properly complete the job.

Fig. 3 - Coil connection.

Fig. 4 - Coil winding direction.

Fig. 5 - Measure separation distance of solenoid or transformer.

Fig. 6 - Replacing or reinstalling secondary winding cylinder
form.
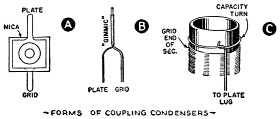
Fig. 7 - Reconnecting winding wires. Creating a "gimmick."

Fig. 8 - Observe direction of windings to ensure proper phasing.
(1) Make a clear diagram of all leads connecting to the coil terminals, marking
the color of each wire and the position that the coil occupied in the receiver.
This should be done carefully and rechecked before, or as, the wires are removed.
(See Fig. 3.)
(2) In removing the leads from the coil, take care to put no unnecessary strain
on the coil terminals lest the lugs move and perhaps break off some lead from a
good winding attached to the lug. If the hook-up wires are hooked through and twisted
around the coil terminal so that it is difficult to get them loose, it is best to
cut the wires, close to the lug. After being cut, the short pieces of wire are usually
easy to remove or, if such is not the case, the ends had best be left attached to
the lugs and the hook-up wire merely soldered to the lugs without going through
or around them when the coil is re-installed.
(3) Carefully examine the defective winding, which is to be replaced, in order
to determine the winding direction and the lugs to which the ends of the winding
connect. This information should be carefully recorded. A convenient method of designating
winding direction is to use an arrow pointing as if its shaft were the outside end
of the coil, and the head of the arrow were the end of the wire. (See Fig. 4.)
(4) The exact location of the winding on the form in relation to the other windings
should be recorded, and the defective winding removed carefully to avoid damage
to other windings or connections. (See Fig. 5.)
(5) If the defective winding consists of only a few turns of wire wound adjacent
to, over, or between the turns of a secondary, this winding can be replaced with
an equal number of turns of No. 36 S.S.E. or 36 D.S.C. wire.
(6) If the defective winding was of the "Universal" or honeycomb type, a (Meissner)
replacement primary should be chosen as near the physical size of the original winding
as possible, and yet be able to slip into place. In some cases, unfortunately, lugs
or other windings interfere with slipping onto the coil form a new winding close
to the size of the defective winding. In such cases a new primary just large enough
to slip over the obstruction should be selected and fastened in place by means of
small hardwood wedges held in place by wax, or "radio cement." (See Fig. 6.)
(Make certain that the winding direction is correct.)
The inductance of the replacement winding selected is determined by the type
of coil being repaired. A Broadcast R.F. coil takes the highest inductance, approximately
7.5 millihenries; an antenna coil for use with an outside antenna takes the lowest
inductance, approximately 1.7 millihenries; while an antenna coil for an inside
or "hank" antenna takes a value between the other 2, approximately 2.25 millihenries.
Since these divisions have been so clearly drawn after a study of the replacement
problems by the Meissner Manufacturing Company, there should be no doubt in the
Serviceman's mind as to which value to select.
(7) Connect the replacement winding leads in accordance with the notes previously
made concerning winding direction and connections.
(8) Check the coil for continuity on all windings and re-install it in the receiver
in accordance with the notes made in section 1.
(9) Align the receiver, and adjust the coupling if necessary as described in
the following paragraphs.
Winding Direction
When a Serviceman is called upon to repair a radio-frequency coil from which
the defective winding has already been removed, or has been so badly damaged that
the winding direction can not be discovered, there are 4 questions that must be
answered:
(1) Which lug was the antenna or plate connection?
(2) What was the probable inductance of the coil?
(3) Where was the winding located?
(4) Which way was the outside end of the winding pointing?
If there is no data to show which lug was connected to the antenna or plate,
the question must be answered from an inspection of the coil, or an answer must
be assumed and the coil repaired and rewired accordingly.
If there is any kind of a coupling condenser used it will be found connected
from the grid end of the secondary to the plate or antenna end of the primary, which
immediately establishes a certain lug as the plate or antenna connection. The coupling
condenser may take the form of 2 metal plates separated by a piece of mica and attached
to the coil form by means of rivets or lugs (Fig. 7A). It may be a loop of
heavy wire circling the secondary near the grid end (Fig. 7B). (This form is
used only with solenoid or bank-wound coils.) It may be a few turns of insulated
wire wrapped closely round another insulated wire forming what is commonly known
as a "Gimmic" (Fig. 7C). In any case, the purpose of the capacity coupling
is to transfer energy from the primary to the secondary.
In the case of "choke coupling," used frequently in R.F. coils, the choke is
either at right-angles to the secondary, or at a considerable distance from it,
and the coupling condenser constitutes the sole means of coupling between primary
and secondary. Unless the coupling condenser is properly wired to the coil and into
the receiver, practically no coupling would exist in the coil concerned. The winding
direction of the primary in this type of coupling has practically no effect on the
gain of the coil, and it may accordingly be connected either way.
In the case where both magnetic and capacity coupling are employed, the purpose
of the capacity is to hold up the gain at the high-frequency end of the band. The
capacity coupling aids the magnetic coupling in such cases. Should a primary be
connected reversed, the capacity coupling would oppose the magnetic coupling and
would produce inferior performance at all frequencies and approximately zero amplification
at some one frequency resulting in decreased sensitivity at all frequencies but
especially poor sensitivity at the one frequency where the magnetic and capacity
coupling cancelled.
In some antenna coils, especially in sets with only 2 sections in the tuning
condenser, the stray capacity between the "hot" end of the primary and the "hot"
end of the secondary is used to buck out the magnetic coupling at some frequency
above the band (in frequency) for the purpose of improving the rejection of interfering
signals in that frequency range. In superheterodyne receivers this improves the
"Image Ratio" of the set. With the exception of this case, which is by no means
universal, the rule for capacity coupling on radio-frequency coils is that the wires
leading away from the coupling condenser must o around the coil form in opposite
directions.
In the event that no physical coupling condenser exists, and no data is available
to tell which were the "hot" and "cold" ends of the primary, the corresponding lugs
should be chosen arbitrarily and the primary connected "capacity aiding," that is
with the wires from the grid of the secondary and the "hot" end of the primary going
around the coil form in opposite directions. (See Fig. 8.)
Alignment
After repairing a coil and re-installing it in the receiver, the circuits should,
of course, be aligned. The normal practice should be followed, using some form of
service oscillator for a signal source, connected through a satisfactory dummy antenna
to the radio set. The usual values of dummy antenna are 200 mmf. for the broadcast
band of sets intended for use with an outside antenna, 85 mmf for the broadcast
band of sets using a "hank" antenna and 400 ohms of resistance for shortwave bands.
If the repaired coil is used on the broad-cast band, the circuits should be aligned
at 1,400 kc. and then "tracking" checked at 600 kc. If the set originally "tracked"
well and the coil has been repaired as directed above, it will "track" well after
the repair. Of course, there is usually no chance to find out how well the set "tracked"
before the repair, but in the case of multiband sets, it is reasonable to assume
that if all of the other bands track well, that the band having the defective coil
also tracked well.
When tracking is poor at the low frequency end of the repaired coil and is good
on all other bands, the coupling on the repaired coil probably needs adjustment,
but if tracking is poor in the same direction on all bands it is probable that the
gang condenser is off its normal value by a small amount.
An experienced Serviceman sometimes bends the plates of the condenser to improve
tracking but this "remedy should not be attempted by some one not thoroughly familiar
with the work, If the plates are bent to improve tracking, the adjustment should
be made on a band that has not had a primary replaced, and then the primary adjusted
on the broadcast band to obtain good tracking at 600 kc.
If the circuit appears to require more capacity at 600 kc. than the gang condenser
supplies, the coupling is too tight and should be loosened by moving the primary
farther away from the secondary; while if the condenser seems to be supplying too
much capacity, the coupling is too loose and should be tightened by moving the primary
closer to the secondary or, in the case of solenoid windings, closer to the center
of the secondary. The latter case is likely to occur when the replacement primary
had to be larger than the original in order to slip over some obstruction.
A convenient method of checking tuning capacity at 600 kc. is to insert between
the plates of the tuning condenser a thin piece of celluloid while watching the
output meter. This adds a little capacity to 1 section of the tuning condenser without
changing the tuning of the other circuits. If the meter reading decreases when the
celluloid is inserted the capacity is too low or the coupling is too tight. If the
meter reading decreases, the capacity may be correct or high. Coupling should then
be tightened until the celluloid slip test just shows too little capacity, and then
loosened slightly.
Conclusion
If care is taken to see that the replacement winding is properly placed (coupling
adjusted if necessary) and proper attention is given to the winding direction and
connections, there should be no difficulty whatsoever to prevent the Serviceman
from giving his customer a satisfactory job in much less time than would be required
to obtain an exact duplicate replacement coil
or to return the defective coil to a coil manufacturer to be repaired or duplicated.
Next month: "Servicing I.F. Coils."
Posted August 9, 2023 (updated from original post
on 6/22/2015)
|