September 1950 Radio-Electronics
[Table of Contents]
Wax nostalgic about and learn from the history of early electronics.
See articles from Radio-Electronics,
published 1930-1988. All copyrights hereby acknowledged.
|
The world is full of
geniuses who have ideas with the potential to introduce history-making products
and services to mankind. Thankfully, many of them manage to draw the attention to
themselves and make their contributions available. Some of those same people have
the talent to prepare their inventions and concepts for distribution, while others
require the know-how of others - nowadays known as manufacturing engineers - to
figure out how to mass produce a product with enough efficiency to make things affordable.
Thomas Edison, Henry Ford, George Westinghouse, Lee De Forest, and other recognizable
inventors depended on assistance for ultimate success. I will soon be posting stories
of De Forest's long, hard-fought path to success with his Audion tube which
will
make you wonder how people can have the fortitude to continue with so many hurdles
placed before them. When reading through this account of television picture tube
production at a Sylvania plant, you have to marvel at how, with the extreme amount
of manual labor involved, it can be profitable. You also have to be impressed with
the skill exhibited by the workers at all stages of the process. There was some
level of automation integrated into the making of the cathode ray tubes, but mostly
everything was assembled and/or processed by hand. Note the lack of personal protection
gear at many work stations. It is no wonder so many people walked around with patches
across their eyes, had scars from mechanical insult or chemical burns, and had missing
limbs and appendages.
The Birth of a Picture Tube: Cover Feature
A complete story in photos of the production of TV picture tubes at the modern
plant of the Sylvania Electric Company in Ottawa, Ohio.

Electron gun mounting section of the picture tube plant.

This automatic stem making equipment seals metal leads into a
glass wafer. The electron gun is then welded to these leads.
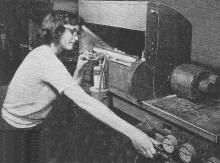
Emissive material is carefully sprayed on the cathodes in the
apparatus in the above photo.

The completed electron guns are being carefully aligned for proper
operation.

Overhead conveyers and other automatic equipment provide a continuous
efficient movement of tubes during production.
|

Once the screens are coated, the conveyer above takes them to
dry.

The first step in making a metal television picture tube is sealing
the glass faceplate to the tube's metal cone.

The operator putting a coat of conductive material on the inside
of a large glass picture tube.

The picture tube bulbs are thoroughly washed to prevent contamination
of fluorescent material.
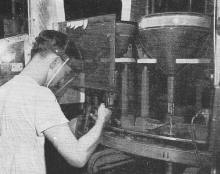
Operator is sealing the nearly completed picture tube after it
has been processed and exhausted. When it is finished, the electrical characteristics
of leach tube must be checked.
|

After coating and screening, the bulbs go through a high-temperature
oven to drive out all organic matter. The operator above takes the bulbs from .the
conveyer as they emerge from the oven and puts them on the overhead conveyer which
takes them on to the next step.

Electron gun mounts and finished glass bulbs are sealed together.
The tube is then ready for exhausting and finishing.

The picture tubes are exhausted, processed, and sealed off in
this new equipment designed for high-speed production.

The operator puts each tube into a test set where light output,
vertical and horizontal scan, focus and many other characteristics are carefully
checked with standards.

Life testing of large TV tubes is a regular practice. These tubes
are run day and night under their maximum ratings.
|
Posted February 6, 2020
|