With a last name like Blattenberger
and an unusually spelled first (Kirt), I learned a long time ago not to poke fun
at anybody's name, but surely the parents of Dr. Hal F. Fruth had a sense of
humor when assigning their little bundle of joy in such a manner (HalF Truth?).
Maybe I assume too much. Anyway, the good doctor published in this issue of
Radio News magazine a very extensive treatise on the art and science of mass
producing radio frequency crystals at a time when the country - and free world -
was in urgent need of them. He notes that, "Prior to Pearl Harbor Day, the world
production of these plates and bars could be counted by the thousands. The present
production rate has skyrocketed more than one hundred fold so that the present production
rate is nearly 30,000,000 units per year." That was in late 1944. World War II
was the epitome of proof for the old adage about necessity being the mother of invention.
The global crystal oscillator market in 2017 was $2.64B and
forecasts predict $3.69B by 2025. Divide those number by any average cost you
please and it represents a huge amount of crystal oscillators.
Crystal Finishing

Dr. Hal F. Fruth
The author, with his colleagues, originated and perfected the mill-finishing
methods discussed here.

Centrifugal beveling machine for beveling and pre-dimensioning crystals after
lapping.
Raw quartz, finished crystal blank, and complete crystal unit.
By Dr. Hal F. Fruth
Assistant Chief Engineer, Research Division, Galvin Manufacturing Company
A discussion of various methods of finishing crystals with particular emphasis
on mill finishing methods including milling time and abrasives.
The piezoelectric crystal is a crystal that is responsive to electric and mechanical
pressures. In its simplest concept, mechanical pressure along one axis gives rise
to dimensional changes and electrical charges on faces perpendicular to the other
axis, and vice versa. This piezoelectric effects finds many uses. This discussion
will be confined to electric oscillators and filters and generally to quartz oscillator
and filter plates and bars.
Prior to Pearl Harbor Day, the world production of these plates and bars could
be counted by the thousands. The present production rate has skyrocketed more than
one hundred fold so that the present production rate is nearly 30,000,000 units
per year. Coupled with this has been a large quality increase and a production cost
reduction, quality for quality, to about one tenth of previous costs. This accomplishment
ranks among the highest of American research, development and production miracles.
The most critical and precise step in crystal production is that of "crystal
finishing," i.e., the last and final operations on the crystal blank to bring it
up to the best activity and the precise frequency, and still produce a surface of
greatest stability. Much has been said about modern precision and "super finish."
High frequency crystal blanks have the smallest thickness tolerance of any existing
manufactured article. In order to finish a BT-cut, 10 megacycle crystal to a tolerance
of ±100 cycles one would have to grind it to ±1 Angstrom unit or ±
4 X 10-9 inches. Stating it another way, ±100 cycles = ±0.01
microinches. The thickness tolerance is equivalent to a very small fraction of a
wave length of blue light and is nearly equal to a layer of quartz one molecule
thick.
Finishing Methods - Hand Finishing
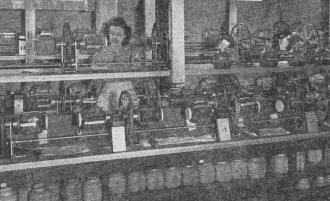
A bank of commercial milling machines for finishing and cleaning
crystals to final frequency.
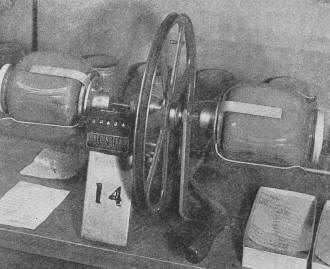
Close-up view of a two-jar machine.

Ten-jar milling machine, with all jars operating from a single
drive.
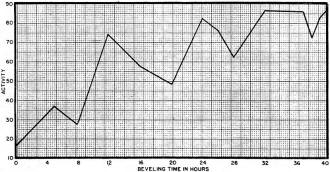
Fig. 1 - Relative activity plotted against beveling time for
a typical crystal.

Fig. 2 - Frequency change plotted against etching time for a
10 mc. crystal lapped with No. 600 silicon carbide. milled 20 kc., and then etched.
Relative activity also shown.

Fig. 3 - Frequency change plotted against milling time for a
5.1 mc. crystal. The relative activity and the change in curvature of the crystal
are also indicated.

Fig. 4 - Plot of frequency change vs. etching time for an 8599
kc. crystal lapped with No. 600 abrasive and then finished by etching. Relative
activity is also shown.
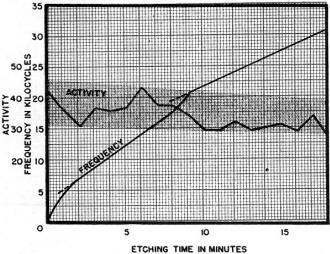
Fig. 5 - Plot of frequency change and relative activity vs. etching
time for a 10,000 kc. crystal lapped with No. 600 abrasive. Break in curve shows
removal of surface layer.
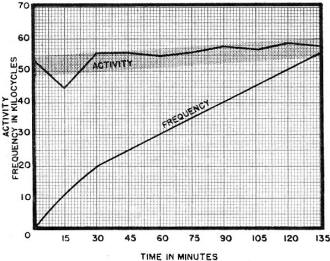
Fig. 6 - Plot of frequency change and relative activity vs. milling
time for an 8170 kc. crystal lapped with No. 600 abrasive and milled with No. 600.
garnet, alcohol and water.

Fig. 7 - Average frequency increase vs. milling time for 8000
kc. crystals milled with quartz, garnet, and Haystellite. 4 to 8 mesh. plus 6% by
volume of No. 600 silicon carbide.

Fig. 8 - Average frequency increase VB. milling time for various
crystals, milled with 4 to 8 mesh Haystellite plus 6% by volume of No. 600 silicon
carbide.

Fig. 9 - Frequency increase vs. milling lime for several individual
crystals milled with 4 to 8 mesh Haystellite plus 6% by volume of No. 600 silicon
carbide.
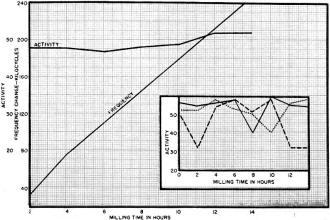
Fig. 10 - Average frequency change and relative activity plotted
against milling time for 6230.4 kc. crystals milled in garnet. Inset shows typical
individual activity curves.
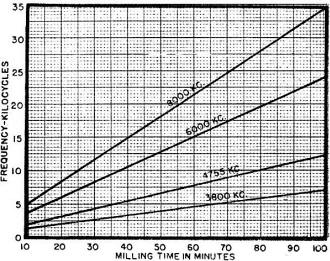
Fig. 11 - Average frequency increase for crystals milled with
4 to 8 mesh garnet and No. 600 silicon carbide, 6% by vol.; 55 r.p.m.

Fig. 12 - Frequency increase per hour as a function of granule
density for 8 mc. crystal. Granules 4 to 8 mesh, plus 6% of No. 600 SiC.

Fig. 13 - Effect of milling on contour of a 4750 kc. crystal.
Contour change for 3 mc. crystal. 0.0002 inch/100 kc. change: 5 mc. 0. 0001 inch/100
kc.: and 8 mc. ... 0.00006 inch/100 kc.
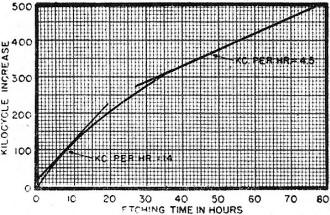
Fig. 14 - Frequency increase vs. etching time for an 8000 kc.
BT crystal etched in 25% "Frequency-Etch" solution.
A few years ago the most generally used method employed for finishing crystals
to final frequency and activity was to rub the crystal by hand over a flat glass
surface coated with a water suspension of very fine emery. A figure-eight motion
was usually used and this grinding repeated on both sides a number of times, the
crystal being washed between measurements. This procedure was repeated a large number
of times coupled with grinding and beveling of the edges until the best activity
and proper frequency was obtained. This procedure required highly skilled "finishers"
who could produce from 30 to 60 crystals per day. Much variation and many uncertainties
were coupled with this method, and, in the light of modern findings, a poorer quality
and less stable crystal and crystal surface was produced. At times, light mechanical
pressure methods were coupled with or substituted for this hand finishing process
with no better results. Even very accurate lapping machines using very light plates,
precise motion and very fine abrasives did not produce a really stable surface.
The surface produced by the so-called "pressure" methods, in spite of its good
appearance under the microscope, was covered with minute cracks, fissures, scratches,
and pits, as well as deeper scratches, often made invisible by being packed full
of a nearly transparent disoriented quartz abrasive, metal and glass, which was
very difficult to remove by washing or scrubbing. However, this foreign material
could be detected by X-ray and could be removed by etching or by exposure to high
humidity temperature and time. This change in the surface of crystals is considered
to be the principal cause of their instability.
Etching
A few manufacturers have for many years finished crystals by etching. The usual
etchant was formerly hydrofluoric acid, with all its hazards and uncertainties.
Recently a number of safer etchants have appeared on the market in the form of liquids,
pastes, or salts, most of them containing a fluoride salt. This method, when used
with good control, is faster and cheaper than hand finishing, lends itself to semi-automatic
mechanical methods and can produce high quality surfaces and crystals when not carried
too far. This method, must, however, be preceded by very careful grinding methods
or processes that produce good smooth surfaces so that the etchant will give predictable
frequency changes and will be prevented from greatly exaggerating cracks, scratches,
etc., which would result in inferior quality crystals, greater fragility, less stable
frequency, and lowered activity. (Figs. 4 and 5.)
Other Finishing Methods
A few laboratories and factories have brought about frequency changes by such
methods as X-ray, heat treatment, and vibration in or on abrasive materials, sand-blasting,
and falling or flowing abrasive on the surface of the crystal. None of these methods
has found extensive use in production.
Mill Finishing or Tumbling
Realizing that the above methods were accompanied by uncertainties and high cost,
and produced inferior surfaces, extensive experiments were undertaken to find a
method for removing quartz from the surfaces of crystals which would be gentle,
random, non-chemical, fast, controllable, "non-custom," predictable and suitable
for mass production.
Such a method seemed to be suggested by a quotation from OVID (43 A.D.).
Gutta cavat
lapidem, non vi sed saepe cadendo, "Not by strength but by constant falling
does the drop hollow out the stone."
It was found that crystals can be put into a pebble or tumbling mill with rather
coarse (4 to 15 mesh) granules and an abrasive powder, and tumbled in a tumbling
jar without breaking or injuring the crystals even when the jar is rotated at speeds
up to 60 rpm. Furthermore, the frequency change is linear with time, and is predictable.

Photographs of crystals finished by various methods, showing
conditions of crystal edges. Left, crystals hand beveled, center, crystals as they
come from lapping and edge grinding machine. and right, crystals machine finished
in the beveling machine.

Table I - Frequency changes of four lots of crystals after various
treatments.
Certain precautions should, of course, be taken and certain variables must be
controlled. It was found that the most important variables were:
(1) Shape and size of the pebble mill, or tumbling container, and the manner
of its rotation.
(2) Speed of rotation.
(3) Size and density of the granules.
(4) Percent of filling of the jar.
(5) Liquid medium and wetting agent.
1. Extensive experiments on the action of the pebble mill showed that in order
to control the thickness of the crystals and not to disturb the outer periphery
and the contour in too large a degree, it was necessary to adjust the charge, the
shape of the vessel, and the angle and speed of rotation, in such a manner that.
the charge would be lifted at an angle without excessive spilling over the upper
surface and would slide down at a point when the angle of repose reaches the critical
value. At that angle, the upper layer slides down in this laver, producing the grinding
action. The crystals would slide over the heavier granules on the top layer and
would experience a relative motion parallel to the faces of the crystals, in a very
highly random motion but under very low pressure. If such a set-up is made, the
contour and the speed of cutting are controllable and predictable.
2. It was found that the rate of change of frequency varied in a nearly linear
manner with the r.p.m., and that a tumbling mill or jar approximately 6" in diameter
having four flat sides and rotating between 10 and 55 r.p.m. gave the best results.
At higher speeds, the crystals, might be injured by being thrown against the sides
too severely, and the cutting action would be cut down.
3. It appeared early in the engineering work that it. was desirable to have two
types of materials with the crystals in the mills, one of them to give weight and
be the force factor, "granules," and the other to do the cutting, a hard, rather
fine material, e.g., 600 silicon carbide. It was found that the rate of frequency
change varied directly with the density of the granules (Fig. 12). However, the
densest material used, 4-8 mesh
Haystellite, was too heavy
for glass jars and was not suitable in general for crystals above 7 mc. Using a
suitable density material for various types of crystals, it was found that the cutting
rate could be varied with the amount of grinding necessary for the crystal in question
and with the delicacy of the wafer or blank.
4. It was found that the amount of charge of the jar was significant; too small
a quantity was not feasible and too large a quantity reduced the cutting rate. It
appeared that a jar five-eighths full of solids gave about the best performance.
5. In order to obtain uniform cutting and obtain clean crystals at all stages,
it was found desirable to add a wetting agent, soap or detergent, such as aerosol
"Alconox"
or some soap which would help to put the fine particles into colloidal suspension,
so that they could be washed away.
It is of utmost importance that no pockets or crevices be present in which crystals
might temporarily be lodged and that no flat surfaces exist, against which they
might be held in any part of the interior of the vessel, in order to assure that
all crystals will receive equal treatment during the entire milling time.
The size of the abrasive seems to influence the cutting rate and the quality
of the surface produced in some degree. However, any silicon carbide or aluminum
oxide in grit sizes from 320 to 800 is suitable for the purpose. The optimum quantity
is usually between four and eight percent by volume of the solid content in the
container. It is desirable to add or renew the abrasive charge every 5 hours, if
the cutting rate is to remain unchanged over many hours.
By omitting abrasive material from the charge and using the granules only, together
with water and a wetting agent and using granule sizes between 10 and 25 mesh, it
was found that crystals could be cleaned very effectively. Tests revealed that in
this manner a very high quality and stable surface could be produced, without the
use of any solvent other than hot distilled water.
Commercial Application
As seen from the graphs (Figs. 6, 7, 8, 9, 11 and 12) the variation of frequency
vs. time is essentially a straight line function, and since the individual crystals
will behave in very nearly the same manner (Fig. 9), the process lends itself readily
to mass production.
A number of procedures may be used; one of them is to take crystals from the
lapping machines, ranging from 100 to 120 kc. away from final frequency, and sort
them into groups of plus and minus 5 kc. each. By referring to the charts for the
frequency in question and the granule and abrasive charge, one can easily estimate
the number of hours necessary to bring the farthest one to the frequency which is
estimated to be from 5-10 kc. away from final frequency.
The other groups are then added in suitable intervals until all groups have been
added, and the mills stopped when it is estimated that all of them are from 5 to
10 kc. short of final frequency. These are now channeled into groups plus and minus
1 kc. and the procedure continued for final adjustment. It is usually desirable
to allow 1 to 2 kc. tolerance for final washing as described above.
Another procedure would be to time each group of crystals in a separate mill
and stop the machines by means of a clock at a time when they arc from 5-10 kc.
away from final frequency.
Contour
It is the belief of many crystal manufacturers that the radius of curvature of
the surface of the crystal, flatness or contour, is of vital importance in the control
of the quality, activity, temperature stability, and harmonic content of the crystal
blank. It was learned, contrary to expectations, that in mill finishing crystals
to frequency there was a continued change in contour, the crystals becoming more
and more flat. Fig. 3 and other experiments indicate that a contour or convexity
of 0.0002" to 0.00005" is more desirable than absolute flatness or a larger convexity.
It is thus possible to allow crystals to become more and more convex during the
lapping processes on lapping machines such as the so-called Hoffman or Atlas laps,
and then allowing the milling process to remove enough quartz to reduce the contour
to the desirable height.
Pre-Dimensioning
Many crystals, particularly those of the BT or AT variety, have to be manufactured
with very great care, surface condition and surface cleanliness being of utmost
importance in insuring high activity and stability with time, temperature and humidity.
The activity at room temperature and the active range of minus 40°C to plus
90°C is active throughout a required temperature function of the dimensions
such as length, width and thickness. These dimensional relationships must be maintained
to very close tolerances. However, in the case of crystal frequencies between 4
and 10 mc. these dimensional requirements are so very exact that it would be practically
impossible to know or maintain them commercially. The random method is therefore
employed. This consists of taking crystals from the mills or from the tumbling machines,
testing them for activity at room temperature and throughout the temperature range,
selecting the satisfactory ones and returning the others for more milling or beveling.
Figs. 1 and 10 indicate the type of curve an individual crystal will follow when
its dimensions are changed very slightly by beveling or by changing its frequency
by milling or other processes. When rejected crystals have been so treated there
is at least a 50% chance that they will be satisfactory. Those that are not yet
satisfactory may receive additional treatment. If the angle of the crystal was correct
and the quartz of proper quality, it is seldom that less than 95% of the crystals
will not eventually respond to this treatment.
In the types of crystals mentioned above, surface conditions and surface cleanliness
are of the utmost importance in order to insure frequency and activity stability
over a long period of time and through a large range of conditions. This surface
must not only be clean but it must be free from imbedded materials pressed into
the surface; it must also be free from minute cracks and injured or disoriented
quartz. There are many methods such as
profilometer, electron
microscope, and X-ray methods of determining the depth of this undesirable layer,
sometimes referred to as the
Beilby layer.
Another method for determining the depth of this layer is to plot frequency change
vs. etching time and note a sharp change of curvature or an abrupt lowering of the
etching rate (Figs. 4, 5 and 14). The point of the beginning of linearity usually
indicates a time when most of the surface "rubble" has been removed. It was found
desirable to etch the crystal to a point where the straight line function begins.
It is to be noted that in these curves, this point lies between 10 and 25 kc. in
one case, and as much as 300 in Fig. 14. This point of beginning of linearity can
be very greatly lowered by proper treatment of the crystal previous to etching.
It has also been observed that there is a general downward trend of activity
with etching time when the surface prior to etching has not been properly prepared
(Fig. 2). It is to be noted there is no downward trend of activity with milling
time even if the crystal has been moved as much as 200 kc. (Fig.10).
In order to determine the life quality of crystals, four varieties of crystals
were prepared and tested, and the results are given in the aging tests (Table I).
Listed are aging results of four lots crystals that were finished to final frequency
in four different manners. They were assembled and placed in a fungus "Tropical
Swamp" humidity chamber for 60 days. The humidity chamber had a temperature of 80°
to 100° F. and 90% to 100% humidity, changed hourly.
Lot #1 crystals were etched 20 kc. to final frequency 8130 kc.
Lot #2 crystals were milled 20 kc. etched 5 kc. to final freq. 8130 kc.
Lot #3 crystals were milled 20 kc. and mill washed 5 kc. to final frequency 8130
kc.
Lot #4 crystals were milled 20 kc. and etched 20 kc. to final frequency 10,000
kc.
It appears from the tabulations that I lot #3 shows the most desirable stability.
The negative changes of many of the groups are probably due to volatile depositions
from the phenolic holder and other foreign matter that had accumulated during the
tests. It is also possible that an etched crystal whose surface was not properly
prepared before hand had etching compounds entrapped in microscopic pits and fissures
which could not be washed out or removed. This could continue to weaken the crystal
without removing materials. Such frequency lowering has been encountered in spite
of great care to keep crystals very clean.
There is much evidence that quartz oscillator crystals can be finished by the
milling method safely and economically, and that the method produces crystals of
equal or superior quality to those manufactured by any other finishing method. It
is particularly superior in all respects to hand-finishing or any other high pressure
method. The method also lends itself very well to combined finishing and beveling
methods and as a preparatory grinding and surface stabilizer prior to etching or
in etch-cleaning processes. Literally many millions of crystals have been treated
and finished by this method or in combination with other methods and are giving
an excellent account of themselves in life tests and in actual service under the
severest service conditions.
|