September 1957 Radio & TV News
[Table
of Contents]
Wax nostalgic about and learn from the history of early
electronics. See articles from
Radio & Television News, published 1919-1959. All copyrights hereby
acknowledged.
|
These days, I'm always a
bit hesitant to publish or do Internet research on items mentioning chemical compounds
any more toxic than rubbing alcohol, lest some digitally eavesdropping
government agency send storm troopers with fully automatic weapons to my house
at 5:00 am to drag my family and me out onto the lawn while in our pajamas. This article reports on early plans of the
Vanguard satellite launch platform for America's first orbiting satellites. Although
the main focus is on the electronic steering and stabilization systems, it mentions
the fuel composition of nitric acid and
unsymmetrical dimethylhydrazine (that sentence alone is probably enough to at least put me on some sort of
surveillance list). Less exotic fuel constituents like
LOX (not
to be confused with the fish used on bagels),
kerosene, and
liquid hydrogen,
which powered most of the man-carrying booster stages, might similarly likely raise a
flag even when taken in context with the article's thesis.
Precision Steering at 18,000 M.P.H.
By Otto Berger
Servo Section, Project Vanguard
The Glenn L. Martin Company
The vehicle that will launch the space satellite is right out of "science fiction",
involving as it does the ability to "think" and cope with the problems of "spacemanship".
At this moment small groups of rocketry specialists in engineering centers across
the United States are pouring the full measure of their sweat and ingenuity into
a project called "Vanguard." Their assignment is to design and test the rocket vehicle
that will launch man's first satellite.
The date of the first launching is fast approaching. President Eisenhower has
announced that the United States will attempt to launch several small, unmanned
earth-circling satellites during the International Geophysical Year, July 1,
1957 to December 31, 1958.
The project is proceeding under management of the Naval Research Laboratory,
supported by agencies of the Army and Air Force. The Martin Company of Baltimore
is prime contractor, charged with responsibility for the design and manufacture
of the vehicle that will place the satellite in its orbit. The National Academy
of Sciences, through the Naval Research Laboratory, will provide the satellite itself
and its instrumentation.
"Project Vanguard" has been hailed by scientists as a mission of great peacetime
promise. Artificial satellites are destined to be man's first observation posts
operating for sustained periods of time beyond the atmosphere. From them will flow
an abundance of new knowledge relating to the earth and the universe.
Yet the day of the satellite would still be a long way off if it were not for
the great strides made recently in rocket propulsion, structural design, and electronics.
A satellite launching system draws upon these technologies to the limits of their
development. "Project Vanguard" then, a forerunner of future progress, is no less
a sign of present achievement.
The "Vanguard" vehicle is a three-stage rocket powerful enough to vault through
the earth's atmosphere to orbiting altitude of 300 miles. If it did no more, the
satellite would immediately fall back to earth. It must, therefore, be able to accelerate
to the amazing velocity of 18,000 miles-per-hour - the rate that offsets the centripetal
pull of gravity at that altitude, and thereby makes orbital travel possible. The
11-ton vehicle must have a means, moreover, of controlling this great lifting strength
and velocity so that the satellite will follow a path that roughly parallels the
earth's contour.
Three big demands are thus laid down for the satellite vehicle. It must lift
the satellite to a height of 300 miles; accelerate it to 18,000 miles-per-hour;
and then - at that altitude and velocity - it must set the satellite free on a path
that approximates a tangent to the earth's surface. That these capabilities may
be built into a single vehicle of manageable size and cost is a tribute to our state
of advancement in rocketry, electronics, and allied fields.

The second stage of the vehicle, shown at left, contains a liquid
rocket engine, designed and built by Aerojet-General Corporation. A gimbal mounting
system and hydraulic actuation units similar to those employed in the first stage
are used for control of the thrust vector during the second stage burning cycle.
The Three Stages
The composite vehicle, resembling a gigantic rifle shell, is about 72 feet long
and 45 inches at its greatest diameter. The first two stages are powered by liquid
propellants and guided by an inertial reference system. The third stage, which carries
the spherical satellite, is powered by solid propellant and is maintained in fixed
orientation while it is firing.
The first stage is a liquid propellant rocket similar to the "Viking" built by
Martin for the Navy, but with substantial improvements. Serving essentially as a
guided booster, it develops most of the energy to raise the remaining stages to
orbital height and about 15% of the required orbital velocity. The engine, built
by General Electric Company, delivers a thrust of approximately 27,000 pounds at
sea level. The major propellants, liquid oxygen and kerosene, are contained in tanks
that are integral with the airframe skin. The rocket motor is fed fuel by turbine-driven
pumps. The pressurizing gas is helium. Control of the vehicle's orientation and
flight path is attained by movements of the engine which is mounted on a gimbal.
In response to autopilot commands, the engine is tilted by electro-hydraulic actuators
to alter the direction of thrust and thus control deviations in pitch and yaw. Roll
control is provided by small auxiliary jet reactors.
The second stage of "Vanguard" carries the entire guidance and control system.
In addition it supplies the remaining energy needed to reach orbital height, and
about 30% of the orbital velocity. It is a liquid propellant rocket that is spliced
to the forward end of the first stage. The propellants, nitric acid and unsymmetrical
dimethylhydrazine, are fed directly to the motor from high pressure tanks integral
with the airframe skin. Again the pressurizing gas is helium. The motor is gimbal-mounted,
as in the first stage, and positioned in pitch and yaw by electro-hydraulic impulses.
An array of jet reactors provides complete control of orientation during second-stage
coasting flight. Forward of these various mechanisms, the second stage houses within
its nose - which is the nose of the entire vehicle - the third stage and the satellite.
The plastic nose cone protects the delicate satellite sphere from the aero-dynamic
heating it would encounter if exposed during the first part of the ascent through
the atmosphere. The cone is jettisoned early in the second stage burning phase,
after which the atmosphere is too thin to be detrimental to the satellite.

Artist's concept of the satellite preliminary trajectory.
The third stage is a solid-propellant, unguided rocket. By approximately doubling
the speed attained by the end of second-stage coasting flight, it imparts the 18,000
mile-per-hour velocity required for the satellite to begin its free-flight orbit
around the earth. In the absence of guidance-jettisoned at the time of second stage
separation - this third stage maintains stability by being spun about its longitudinal
axis in the manner of a rifled shell. While still attached to the second stage,
it is mounted on a turntable, or spinning mechanism. Near the end of second-stage
coasting flight, the turntable is set in motion by small solid propellant rockets.
When the third stage is. spinning, retro-rockets fire-retarding the flight of the
second stage shell. The momentum of the third-stage-satellite combination, however,
remains unchecked. Thus freed, the final rocket begins its powered flight.
The satellite payload, a 20-inch sphere, is attached to the forward end of the
third stage, and may be separated when orbital velocity has been attained. As the
third stage will reach orbital velocity, when separated from the payload, it also
will become a satellite.
Orbital Characteristics
Even at altitudes of 300 miles and above there is a minute drag. Over a period
of time this drag will retard the satellite's velocity and thus lower its altitude,
so that it will describe a de-celerating, descending spiral. When it descends to
atmosphere of sufficient density, the satellite will burn and dis-integrate. Based
on present estimates of densities, scientists at the Naval Research Laboratory calculate
that the satellite could exist in a circular orbit of 300 miles height about one
year. If the height varies from 200 to 1500 miles at the lowest and highest points
(perigee and apogee), the lifetime would be only 15 days. A 100-mile perigee would
end the satellite's career within an hour.
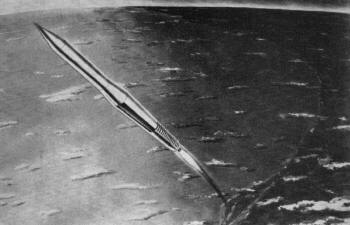
The first stage (portion of complete vehicle shown at the right)
is powered by a liquid rocket engine, employs liquid oxygen and kerosene as fuels.
The thrust cylinder extends aft of the rocket structure. This cylinder is moved
by hydraulic actuators in a gimbal system so that flight path control is possible.
The preferred orbit - a nominal circle 300 miles above the surface of the earth
- could be attained only if the angle and velocity of firing were controlled perfectly.
Inevitable control errors, however, will result in an elliptical orbit.
It is intended that the initial orbit will lie between 200 and 1500 miles altitude.
A greater apogee would hinder optical tracking while a perigee below 200 miles would
seriously reduce the life span of the man-made moon.
Control System
Correct angle of injection depends on correct functioning of the control system
which steers the "Vanguard" vehicle over the predetermined trajectory. It employs
a magnetic amplifier autopilot working in conjunction with an inertial reference
guidance system. The course is set into the system before launch and played back
via a master sequence controller which initiates each phase of flight at precisely
the right moment. It is thus unlike other guidance systems that employ radar to
track the rocket, issuing steering commands from the ground with the help of a computer.
All control equipment is located in the electronic section of the second stage.
Heart of the guidance system is a trio of single-axis, rate-integrating gyros. One
is aligned with the "yaw" axis, another with the "pitch" axis, and the third with
the "roll" axis. Once set and stabilized in a particular plane, the gyros remain
fixed in that plane despite contrary movements of the vehicle. Roll and yaw orientation
are fixed, while the pitch reference is pre-programmed to establish the curving
trajectory planned for the rocket.

This is the equipment that will be used to launch the satellite-carrying
Vanguard three-stage vehicle. The structure in the background is a gantry crane
used to erect and assemble the vehicle and to provide work platforms from which
the field crew can test the rocket prior to launch. At the lower right is the concrete
blockhouse from which the rocket operation is monitored prior to and during flight.
All final tests are remotely performed by personnel locked in the blockhouse and
when the rocket is ready for flight it is fired from this remote location. As seen
in this sketch, the Vanguard launch stand does not include a pit to conduct exhaust
gases away from the rocket but rather the vehicle itself will be elevated and steel
exhaust duct provided. The rocket will be finless and stabilization will be achieved
by use of a gimbaled engine. Omission of fins saves weight.
Let's say the heading of the vehicle changes from the desired direction because
of a gust of wind, sloshing of fuel in the tanks, or irregularity of the rocket
engine. The deviation is sensed by the yaw gyro, which remains set on the correct
course. The gyro sends out proportionate electrical signals to the autopilot, which,
operating through electro-hydraulic actuators, causes the rocket controls to bring
the vehicle back on course. Deviations in roll and pitch are corrected in similar
fashion.
The phase lead required to stabilize the rocket is produced by operational networks
that introduce a phase lag in the feedback circuit of the amplifiers.
Using the conventional equations for a feedback amplifier:

where: Kƒ=gain with feedback
K = forward gain

where: Kb is a function of the number of turns on the feedback winding
and the values of the resistances.
On substitution we obtain: 1 + (RCS/2)

When compared with a conventional lead circuit, this equation shows that the
time constant, T, is given by (RCS/2) and the attenuation by 1 + KKb.
Velocity Measurement
The all-important velocity of the "Vanguard" vehicle is measured by an integrating
accelerometer installed in the second stage electronics section. The instrument
senses the acceleration applied to the vehicle during flight, sums it up, and thus
yields the velocity. The velocity measurement made at the end of the burning of
the second stage is supplied to the unit's analogue computer, which determines how
long the vehicle will coast before the third stage, carrying the satellite, is fired.
The basic component is a floated gyro. An acceleration on its sensitive axis
generates a signal which, when amplified, drives a turntable which rotates the gyro
about its input axis. The resulting torque is equal and opposite· to the acceleration
torque. Since the turntable turns at a rate proportional to acceleration, its position
is proportional to the integral of acceleration, or velocity.
The relation between torque and input, angular velocity depends on the angular
momentum which, in turn, depends on the power frequency. There is no means of compensating
for changes in frequency. Consequently, since the frequency of the 400 cps supply
is not controlled accurately enough, it is necessary to generate an accurate 400
cps. This is done by means of a tuning fork whose output is amplified in a transistor
amplifier to drive the gyro.
Posted April 10, 2023 (updated from original post
on 8/26/2014)
|