May 1971 Popular Electronics
Table of Contents
Wax nostalgic about and learn from the history of early electronics. See articles
from
Popular Electronics,
published October 1954 - April 1985. All copyrights are hereby acknowledged.
|
Following the previous
month's introduction to "Chemicals for Electronics,"
which covered degreasers, cleaners, and polishing agents,
author Lon Cantor in the May issue of Popular Electronics wraps up with coolers, lubricants,
and special agents (no, not spies) such as protective and insulating coatings. He
devotes a lot of space to freeze spray for use in troubleshooting problems
caused by overheating circuit components. In the days before comprehensive
computer aided design environments that can identify heat concentrations with
detailed temperature maps and design rules checks (DRC), predicting potential
overheating sources in both normal operation and during impending failure was
much more difficult. Running a large series of worst case scenarios on actual
hardware and monitoring multiple areas of circuitry was too time consuming and
expensive to do for non-critical applications (as opposed to things like life
support and space operations). My point is that the likelihood of
overheating-induced failures is less likely with today's products when proper
design and operation is conducted. Freeze spray was an indispensable resource
for both troubleshooting and design prototyping before such computer methods
were available.
Chemicals for Electronics - Part 2 of a 2-Part Story
Getting to know coolers, lubricants and
special agents
By Lon Cantor
Last month on these pages we expressed some surprise that so few electronics
experimenters make use of the many chemical aids available to them from jobbers
and distributors. This is particularly true if the experimenter has encountered
the so-called "tough dog." Technically, the TD is an intermittent - a circuit defect
that can drive hobbyists wild with frustration.
Intermittents pop up when your equipment works well for 10 or 15 minutes, then
loses power, generates distortion, becomes erratic, or quits altogether. The problem
is that as you try to track down the trouble, it moves off in another direction.
Fortunately, most TD's are related to heat and can be tamed by using a simple chemical
tool - an aerosol can of component cooler.
Thermal Intermittents. There are two basic types of thermal
intermittents: (1) components that work properly only when they are hot, and (2)
components that work properly only when they are cool. Some resistors, for example,
start off in fine shape when they are cool, but rapidly change in value when heated
up. If you check circuit voltages when the equipment is hot, you may obtain all
sorts of "wrong" voltage readings. When the equipment is turned off and the resistors
are checked with an ohmmeter, all the readings are good - since in most instances
the resistor has cooled down enough to look normal.
In some instances, solid-state devices will have internal metallic contacts that
tend to open when the ambient temperature rises. On the other hand, some components
have hairline cracks or contacts that do just the opposite: open up when the component
is cool. The latter sort of intermittent (enclosing the crack or contact after the
equipment has been turned on) is probably one of the most frustrating problems.
Special Chemicals

Heat Eliminating Gel
One of the "strangest" chemicals that the hobbyist/experimenter may want to try
is Cool-It-Gel sold by Dynatek lndustries, Box 24268, Cleveland, OH 44124. This
jelly-like substance is a pale blue viscous mix that is brushed, dipped or fashioned
like putty to make a heat sink! If, for example, some of the Cool-It-Gel is "puttied"
around transistor leads ready for soldering, the Gel will protect the transistor
by dissipating the heat. The Gel itself gradually disappears and will not run, drip,
prove to be toxic, create fumes, etc. The manufacturer recommends Cool-It-Gel for
electricians and welders working in tight quarters or with delicate components.
A trial pint is $2.95, postpaid.
No matter what the cause of the failure, all thermal intermittents can be tracked
down with a good freezing spray. However, beforehand, take the following steps:
A. Based on the symptoms and your understanding of how the equipment
works, use flow logic to isolate the trouble to one or two stages.
B. If the equipment is vacuum-tube operated, replace all the
tubes in the suspected stages. Don't test the tubes because intermittents are seldom
detectable on a tube tester.
C. Apply power to the equipment and heat it up as rapidly as
possible. Some technicians cover equipment with a cardboard box to speed heating
in the absence of ventilation. Let the equipment operate until the trouble either
appears or disappears and at this point you have a chance of proceeding with your
troubleshooting.
Use a chilling spray with an extension tube to spray each resistor, capacitor,
and semiconductor individually. Keep the spray away from vacuum tubes - a cold spray
can easily crack the glass envelope. When you note a dramatic difference in circuit
performance, you'll know you have spotted the culprit. Spraying the faulty component
with the cooler should turn the trouble on or off like flipping a switch. Replace
the faulty component and "cook" the equipment for at least an hour. Respray the
new component to make sure that you have really located the trouble.
Special Chemicals

Quick Bonding Liquid
Zipbond Contact Cement distributed by Tescom Corp., Instrument Division, 2633
S.E. 4th St., Minneapolis, MN 55414 is one of the most unusual chemicals available
to the advanced hobbyist and experimenter. It may be used to bond a wide range of
materials - metals, plastics, glass, rubber and hard woods. There is no mixing or
heat treating - simply apply a drop of liquid for each square inch of surface to
be bonded. Apply light pressure for about a minute and a bond of very high shear
strength is made. Zipbond is expensive ($15.95/oz), requires careful use, and should
be refrigerated when being stored.
Other Component Cooler Uses. Aside from locating thermal intermittents,
component coolers arc excellent for finding hairline cracks on printed circuit boards.
Cracks are a real nuisance, since you can't see them with the naked eye unless you
know precisely where to look. A good component cooler will help you spot the trouble
fast. Simply spray the cooler (without the extension tube) over the suspected circuit
board. The areas covered by printed conductors will frost up, turning white. The
areas without the etched conductors won't change color. Any crack in a conductor
will look like a thin, dark line and should - stand out prominently.
Aerosol freezing sprays make an excellent soldering aid. They can be used to
protect delicate components such as transistors, diodes, and integrated circuits
which might be damaged by the heat of soldering. Spray the component, chilling it
thoroughly and you won't have to worry about using a heat sink. Many experimenters
also use component coolers to prevent cold soldered joints. Once the solder is flowing
freely and the connection has been made, they give the new joint a quick blast of
the chilling cooler. This blast quickly absorbs the heat from the solder and eliminates
the possibility that something might move before the solder has set. Also, the cooler
washes away excess rosin and residue, leaving a clean, bright, soldered joint. Certainly
this method is far preferable to the practice in many laboratories of cooling the
solder joint with a little spit at the end of your finger.
A freezing spray can also be used to rescue a power transformer. Experimenters
sometimes fire up circuits only to see the power transformer start to smoke. When
this happens, pull the plug fast and reach for your aerosol cooler. If you chill
the transformer fast enough, you will keep the wax, varnish and shellac from running
and causing internal shorts in the transformer windings.
Choosing a Component Cooler. With all the component coolers
on the market, how do you choose the right one? The best coolers are made with blends
of Freon. As mentioned in the first part of the story, Freon is Dupont's trademark
for trichlorotrifluoroethane. This product is used both as an aerosol propellant
and as a cleaning agent. Special blends of Freon are excellent as coolers working
on much the same principle as a refrigerator - a liquid changed to a gas absorbing
a tremendous amount of heat. A good component cooler can drop the temperature of
a small component to minus 50 degrees Fahrenheit in a matter of seconds.
Some manufacturers of component coolers for the sake of economy will add vinyl
chloride to their product. Vinyl chloride is cheaper, but does not cool as well
as Freon and, what's worse, tends to run (cooling unwanted components). It also
has the undesirable after-effect of leaving a residue. You can usually detect the
presence of vinyl chloride in a circuit cooler with your nose - it smells sharply
of chlorine.
Oddly enough, packaging makes a difference in component coolers. Freon products
are packed, under high pressure and must be in a seamless can. Aerosol cans with
seams simply can't hold this amount of pressure and for safety, the law requires
the use of seamless cans for all high pressure applications. Coolers packed in seamed
cans or using vinyl chloride do cost less, but in most cases, this is considered
to be a false economy. For one thing, inadequate cooling can cause you to skip right
over a defective component and the better products can chill more components per
ounce of cooling fluid.
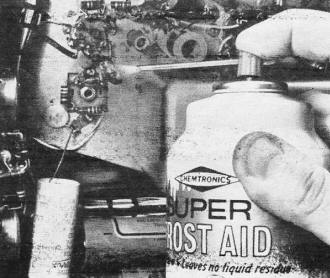
Loss of gain and erratic operation reo suited from manufacturing
defect in bypass capacitor. Tipoff was gradual loss of signal after receiver had
been in operation for an hour. Cooling down suspect components with freezing spray
quickly pin-pointed defective capacitor.
Lubricants. The experimenter with a home workshop has an incredible
variety of lubricants available to him from electronics parts distributors and hardware
stores. The most common lubricant are of the type known as all-purpose, penetrating
and lubricating oils. Made from petroleum bases, these lubricants are excellent
for freeing rusted parts, as well as reducing friction in motor bearings, couplings,
etc. Most of these lubricants tend to retard rust and many are available not only
in drop cans, but as aerosols.
Some of the more unusual lubricants that should be investigated by the experimenter
include white grease, dry graphite and silicones. White grease is excellent for
small motors, gears and bearings and is available in small squeeze tubes. Graphite
has been used in a powder form for locks and is now available in aerosol cans. Silicone
lubricants are very slippery, wear well, and usually seal out moisture. These lubricants
are also available in aerosol cans and function very well over a wide range of operating
temperatures.
A Teflon dry lubricant is now available in an aerosol can and, is used where
very high operating temperatures are encountered. Cryogenically processed Teflon
is also used, although it is not commonly available to most experimenters.
Insulating and Protective Coatings. No electronics experimental laboratory workbench
is complete without a bottle of brush-on insulating coating (or varnish) and an
aerosol can of acrylic protective spray.
Brush-on insulating coatings are particularly useful around high-voltage circuits
where they can be used to stop arcing and corona. These coatings can also be used
for "potting" components, holding high voltage leads in place, insulating PC boards,
and making temporary repairs to exposed wiring.
Acrylic insulating and protective sprays may also be used to coat low voltage
exposed wiring, waterproof spark plug cabling in ignition systems, inhibit rust
and corrosion on exposed surfaces, act as a protective coating for outdoor antennas
(especially in areas where there is salt spray or industrial smog), and/or retard
fungus and mildew. Although most of the crystal-clear acrylic sprays are available
in aerosol cans, you can also buy a viscous acrylic liquid in a bottle and apply
it with a brush. In many instances, the latter method is to be preferred - especially
when working in tight corners.
Posted April 15, 2019
|