January 1957 Popular Electronics
Table of Contents
Wax nostalgic about and learn from the history of early electronics. See articles
from
Popular Electronics,
published October 1954 - April 1985. All copyrights are hereby acknowledged.
|
According to a 2001 paper
published by the National Institute of Standards and Technology (NIST, formerly National Bureau
of Standards, NBS), "The end of the era of quartz frequency standards began in 1949
with the development at NBS of the world's first atomic frequency standard based
on an ammonia absorption line at 23.87 GHz." Further, "The Bureau supported
work on both technologies for the next decade, but the rapid advances in the accuracy
of atomic frequency standards could not be matched by quartz devices, and the work
on quartz frequency standards was stopped in 1959." This article from a 1957 edition
of Popular Electronics magazine claims that the "master of all master-clocks" resided
at the U.S. Naval Observatory at the time - not quite accurate from what my research
indicates. Still, it is a good introduction to crystal growth and processing for
use as timing devices.
After Class: Special Information on Radio, TV, Radar, and Nucleonics
Some Facts on Quartz Crystals
In the U. S. Naval Observatory at Arlington, Va., is the master of all master-clocks.
The primary standard for all the timepieces of the nation, this clock is never fast
or slow by more than a few seconds in one-hundred million. If you were to measure
the distance between New York and Miami, Florida, with this kind of accuracy, the
results would not be in error by more than the length of one standard cigarette!
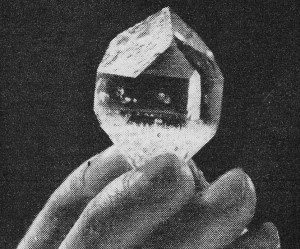
Synthetic quartz mother stone was grown in a laboratory. Bell
Telephone labs.

Thin wafers are cut from large mother stones by multiple saw.
Wafers must then be ground and polished. James Knights Co.
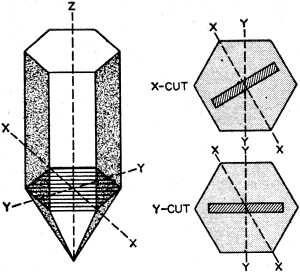
Fig. 1. Axes of mother stone and orientation planes of X-cut
and Y-cut crystal blanks. A hexagonal prism has six X and six Y axes.
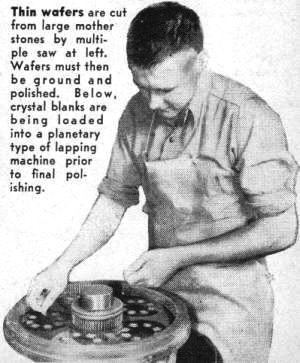
Crystal blanks are being loaded into a planetary type of lapping
machine prior to final polishing.
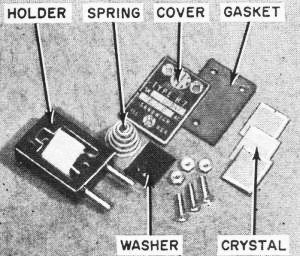
Disassembled military type FT-243 (7620-kc.) pressure-sandwich
type of crystal holder used extensively in communications equipment.

Fig. 2. Analogy showing relation of overtones to fundamental:
(A) a string producing its fundamental tone by vibrating in one part; (B) first
overtone or second harmonic of the string; (C) second overtone or third harmonic.
Such fabulous micro-precision, matched only by the earth itself as it spins on
its axis, is keyed to a tiny slab of crystalline quartz held under rigid temperature
control in a special oven. Although it may soon be supplanted by an even more precise
time standard (resonance of cesium atoms), the quartz crystal still remains the
most important frequency-controlling device in existence today.
How They Are Cut
Oscillating crystals are cut from so-called mother stones by high-speed carborundum
wheels. Although most finished plates come from natural quartz prisms, modern techniques
for growing mother stones in the laboratory have been perfected to the degree where
our dependence upon nature soon will be unnecessary. Synthetic crystals are often
superior to natural ones since the conditions during synthesis are held under rigid
laboratory control.
A crystal exhibits piezoelectric activity. This means that it develops electric
charges on its faces when compressed or otherwise distorted in shape. When connected
in the grid circuit of a vacuum tube, sustained oscillations of one particular frequency
are produced. Since the thickness of the crystal plate is an important factor in
determining the frequency of oscillation, the cut blank is ground and polished until
its mechanical resonant frequency arrives at the desired value; the thinner the
crystal, the higher its resonant frequency.
At one time, only X-cut and Y-cut crys-tals were available. These terms indicate
that the crystal slices are taken from the mother stone at right angles to the X
and Y axes. The X-axis is a line joining two opposite corners of the hexagonal prism
and the Y-axis is a, line joining the mid-points of the two opposite faces. (See
Fig. 1.) Both of these cuts are subject to temperature effects, changing frequency
over relatively wide ranges as the temperature varies.
Between 1934 and 1949, vastly improved cuts were discovered by scientists connected
with Bell Telephone Laboratories and RCA. Labeled AT, BT, V, CT, and DT, these crystals
were ground from blanks oriented at complex angles with the axes of the mother stone.
Finally, in 1940, the most stable quartz crystal ever devised was announced by W.
P. Mason. Known as the GT-cut, this crystal shows no appreciable change in frequency
from -25° C to +75° C; the cut remains virtually "on-frequency" over a range
of 180° F!
The kind of cut you might use depends upon the depth of your purse and its contents.
X- and Y-cuts are quite inexpensive while a GT-cut for a specific frequency is still
prohibitive in cost to experimenters of average means.
Characteristics
The most important single crystal parameter is its temperature coefficient. Since
the frequency of a Y-cut crystal rises with temperature, it is said to have a positive
coefficient; conversely, the coefficient of an X-cut crystal is negative because
frequency drops with rising temperature.
For example, the temperature coefficient of a certain Y-cut crystal is given
as +75 p/m/C°. This is read as "plus 75 parts per million per °C." It means
that for every degree rise in temperature, the crystal frequency rises 75 cps for
each megacycle of its basic frequency. Thus, if you assume that the temperature
of this Y-cut crystal ground for 3 mc. at 0° C goes up 10° C, the change
in frequency will be: 75 cps X 3 mc. X 10° = 2250 cps = .00225 mc. Adding this
to the basic frequency gives 3.00225 mc. On the surface, this does not appear to
be a serious deviation, but it is a change of 750 parts per million for only 10°
of temperature variation. The GT-cut, on the other hand, varies only one part per
million over a 100° C range (180° F).
For any given cut at a specified temperature, the frequency of oscillation is
determined by the thickness of the blank. As a crystal is ground thinner and thinner,
its natural frequency rises. In the early days of crystal control, it was virtually
impossible to grind the quartz slabs thin enough to exceed 20 mc. without having
them fracture during operation. Since some cuts are worse than others in this respect,
the thickness-frequency specification for each is given in terms of the frequency
factor. This parameter is defined by the simple equation: k: = F X t; where F is
the fundamental frequency of the crystal in mc., t is the thickness in thousandths
of an inch, and k is the frequency factor of the particular cut.
For example, the X-cut has a frequency factor of approximately 112 while the
Y-cut is rated at 77. Suppose that one of each of these were to be ground to oscillate
at 4 mc. Their respective thicknesses would be:
X-cut: t = k/F = 112/4 = .0028"
Y-cut: t = k/F = 77/4 = .0019"
From this it is evident that the larger the frequency factor of a crystal, the
thicker it may be for a given frequency. The AT-cut, with a frequency factor of
about 66, is just about the thinnest of all plates.
Overtone Crystals
An overtone or harmonic quartz crystal is one that has been specially ground
or otherwise treated by the manufacturer so that it vibrates in two or more parts
rather than as a whole. Essentially, this process is very similar to overtone production
in musical instruments where the sounding body vibrates in parts showing nodes and
loops along its length (Fig. 2). If a crystal were to vibrate in two equal
parts, the output would be exactly double the fundamental or "one-part" frequency.
In practice, this is seldom the case, because overtone crystals do not "break up"
into equal sections as they oscillate.
If, for example, an AT-cut crystal is treated to produce third harmonic output
at 21 mc., it might be marked "7-mc. fundamental" This means that its harmonic frequency
is approximately three times its fundamental; its output may differ from the true
third harmonic by several megacycles. When such crystals are purchased for transmitter
control, the buyer should know the harmonic output rather than the fundamental frequency.
Overtone crystals are almost always used in special oscillator circuits in which
the crystal responds at its series resonant frequency. Standard oscillators operate
at their parallel resonant frequencies.
Mounting. The development of better crystal holders has kept pace with improvements
in the fabrication of finished quartz plates. These holders are designed to avoid
interference with the piezoelectric vibrations of the crystal and to provide protection
against mechanical shock. In the pressure-sandwich type of holder, the crystal is
supported between two electrodes which are in intimate contact with a pair of flat
metal plates to insure good electrical connection. Spring loading and the use of
fiber and neoprene make for firm support, excellent protection, and hermetic sealing.
This type of holder typifies medium-frequency mounting techniques; at the higher
frequencies, particularly when overtone crystals are employed, other kinds of holders
are favored.
For extra-precise control of frequency, crystal holders are often enclosed in
thermostatically controlled ovens which maintain the frequency constant over extremely
wide variations in ambient temperature. Such holders are very compact and weigh
only a few ounces.
Four types of mountings. At left is a 110-kc. X-cut crystal in a
military type HC-13/U holder which produces very little damping and some mechanical
resonance in wires supporting the crystal. Next is a GT-cut in a special holder;
the crystal is first plated with gold, then placed in evacuated glass holder, and
is supported by eight wires soldered to plating. In cutaway view, a circular, silver-plated
AT-cut in a glass holder is mounted inside temperature-controlled oven for greater
stability. At right is a close-up view of an NT-cut in a miniature glass holder
supported by four wires.
"After Class" Topics
|